Technique for synthesizing vitamin A aldehyde
A synthesis process and vitamin technology, applied in the field of vitamin A aldehyde synthesis process, can solve the problems of catalyst deactivation or decomposition and damage, affecting the effect of the catalytic system, etc., and achieve the effects of fast reaction speed, stable catalyst and high catalytic activity.
- Summary
- Abstract
- Description
- Claims
- Application Information
AI Technical Summary
Problems solved by technology
Method used
Image
Examples
Embodiment 1
[0020] First prepare 4-methoxy-1-oxo-2,2,6,6-tetramethylpiperidine, in 1000ml there is a three-necked flask with stirring, dropping funnel and condenser, add 87g (0.5mol) 4-hydroxyl-1-oxo-2,2,6,6-tetramethylpiperidine, add 600ml THF, add 20g of NaH (60% content, 0.5mol) while stirring under the protection of nitrogen, there is a large amount of After stirring for 1h, add 38mL (0.6mol) of MeI dissolved in 100mL THF dropwise at 0°C. After 1h, the solution is orange-red and solids are formed. The mixture is reacted at room temperature for 5h , after removal, add 1500ml of ether, wash with ×100ml of water, separate the ether, and use anhydrous MgSO 4 After drying, diethyl ether was distilled off under normal pressure to obtain a viscous red liquid, which was added to 200 mL of n-hexane and stored at -20°C. 136 g (yield: 72.5%) of needle-like crimson crystals crystallized out, melting point: 42-43°C.
[0021] Then synthesize vitamin A aldehyde, first put 100 grams of vitamin A alc...
Embodiment 2
[0023] First prepare 4-ethoxy-1-oxo-2,2,6,6-tetramethylpiperidine, in a 250ml there-necked flask with stirring, dropping funnel and condenser, add 17.4g (0.1mol ) of 4-hydroxy-1-oxo-2,2,6,6-tetramethylpiperidine, add 100ml THF, add 4.0g (0.1mol) of NaH while stirring under the protection of nitrogen, there are a lot of bubbles After stirring for 1 h, C dissolved in 30 mL THF was added dropwise 2 h 5 I 9.2mL (0.13mol), drop by drop at 0°C, drop after 1h, the solution is orange red, and a solid is formed, the mixture is reacted at room temperature for 5h, add 400ml of ether, wash with 2×50ml of water, separate Ether layer, with anhydrous MgSO 4 After drying, diethyl ether was distilled off under normal pressure to obtain a viscous red liquid, which was added to 40 mL of n-hexane and stored at -20°C, and 25 g of needle-like crimson crystals crystallized out, melting point: 35-36°C.
[0024] Then synthesize vitamin A aldehyde, first put 100 grams of vitamin A alcohol (yellow cr...
Embodiment 3
[0026] First prepare 4-methoxy-1-oxo-2,2,6,6-tetramethylpiperidine, in 1000ml there is a three-necked flask with stirring, dropping funnel and condenser, add 87g (0.5mol) 4-hydroxyl-1-oxo-2,2,6,6-tetramethylpiperidine, add 600ml THF, add 20g of NaH (60% content, 0.5mol) while stirring under the protection of nitrogen, there is a large amount of After stirring for 1 h, 38 mL of MeI (0.6 mol) dissolved in 100 mL of THF was added dropwise at 0°C. After 1 h, the solution was orange-red and a solid was formed. The mixture was reacted at room temperature for 5 h. After removal, add 1500ml of ether, wash with ×100ml of water, separate the ether, and wash with anhydrous MgSO 4 After drying, diethyl ether was distilled off under normal pressure to obtain a viscous red liquid, which was added to 200 mL of n-hexane and stored at -20°C. 136 g (yield: 72.5%) of needle-like crimson crystals crystallized out, melting point: 42-43°C.
[0027] Then synthesize vitamin A aldehyde, first put 100...
PUM
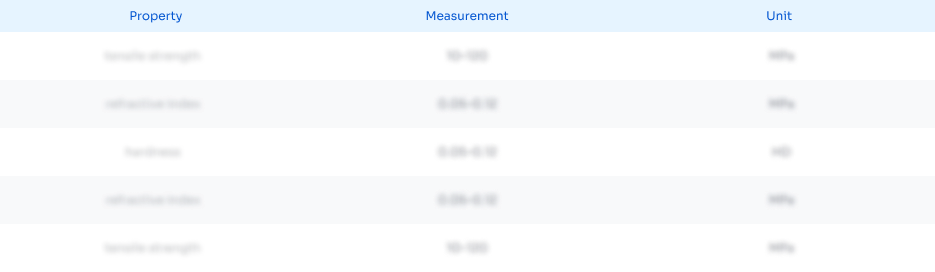
Abstract
Description
Claims
Application Information

- R&D Engineer
- R&D Manager
- IP Professional
- Industry Leading Data Capabilities
- Powerful AI technology
- Patent DNA Extraction
Browse by: Latest US Patents, China's latest patents, Technical Efficacy Thesaurus, Application Domain, Technology Topic, Popular Technical Reports.
© 2024 PatSnap. All rights reserved.Legal|Privacy policy|Modern Slavery Act Transparency Statement|Sitemap|About US| Contact US: help@patsnap.com