Method for preparing polyacrylonitrile-based carbon fiber protofilament
A technology of polyacrylonitrile-based carbon fiber and polyacrylonitrile resin, which is applied in the field of producing polyacrylonitrile-based carbon fiber precursors by solution spinning process, and can solve problems such as shortage
- Summary
- Abstract
- Description
- Claims
- Application Information
AI Technical Summary
Problems solved by technology
Method used
Image
Examples
Embodiment 1~10
[0040] The polyacrylonitrile resin, which is the raw material for spinning, is soaked and swelled in deionized water, the water temperature is controlled in the required temperature range, soaked and swelled to the required time, and then taken out to remove excess water. See Table 1 for the process conditions of soaking and swelling;
[0041] The soaked and swollen polyacrylonitrile resin is placed in an aqueous acid solution and stirred for pickling. Embodiment 1~8 adopts nitric acid, and embodiment 9~10 adopts hydrochloric acid, and other pickling process conditions are shown in Table 1;
[0042] Then the polyacrylonitrile resin is rinsed to neutrality with deionized water, and the rinse water temperature is shown in Table 1;
[0043] Finally, the polyacrylonitrile resin is dehydrated by vacuum filtration, and dried at a temperature of 80-100°C until the moisture content of the resin is lower than 3%.
[0044] The ash content and Na ion content of the polyacrylonitrile re...
Embodiment 11~17
[0052] The polyacrylonitrile resin of embodiment 1~10 washing treatment adopts conventional technology to carry out solution spinning, and the steps are as follows:
[0053] Mix the washed resins of Examples 1-10, dissolve them in a solvent to make a spinning stock solution, the solvent is 35-58 wt% NaSCN aqueous solution, and the content of polyacrylonitrile resin in the spinning stock solution is 8-16 wt%;
[0054] The spinning stock solution is spun after removing air bubbles, and is coagulated by a coagulation bath to form nascent fibers. The coagulation bath is 8 to 16 wt% NaSCN aqueous solution, and the temperature of the coagulation bath is controlled between -5 and 16 °C;
[0055] The as-spun fibers were rinsed with deionized water, and the water temperature and rinse time were shown in Table 3;
[0056] The nascent fibers are pickled in an acidic water bath, and the acid is nitric acid or hydrochloric acid, wherein Examples 11-14 and 16-18 are nitric acid, and Example...
Embodiment 18
[0061] The as-spun fibers are directly drawn after pickling, and the drawing is heated by a hot water bath, and the rinsing process is carried out simultaneously with the heating and drawing process in the drawing hot water bath. The drawing hot water bath is deionized water, the temperature of the drawing hot water bath is the same as that of the rinsing hot water bath, and the residence time of the as-spun fibers in the drawing hot water bath is the same as the rinsing time.
[0062] Except above-mentioned, all the other are with embodiment 11~15. Determination of the ash and Na ion content of the raw silk product, the results are shown in Table 4.
[0063] table 3.
[0064]
[0065] Table 4.
[0066] Raw silk ash
PUM
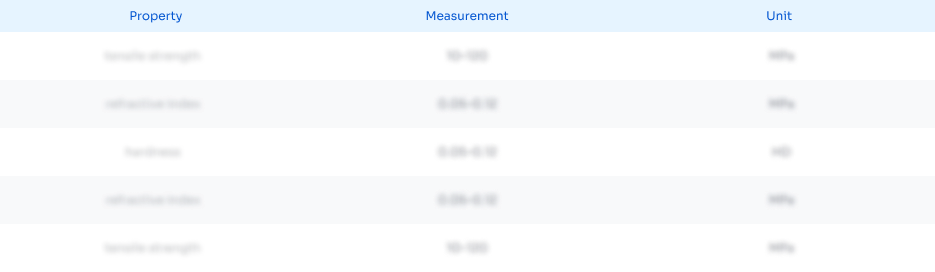
Abstract
Description
Claims
Application Information

- Generate Ideas
- Intellectual Property
- Life Sciences
- Materials
- Tech Scout
- Unparalleled Data Quality
- Higher Quality Content
- 60% Fewer Hallucinations
Browse by: Latest US Patents, China's latest patents, Technical Efficacy Thesaurus, Application Domain, Technology Topic, Popular Technical Reports.
© 2025 PatSnap. All rights reserved.Legal|Privacy policy|Modern Slavery Act Transparency Statement|Sitemap|About US| Contact US: help@patsnap.com