Method for preparing ceramic composite wood
A ceramic and wood technology, applied in wood treatment, wood impregnation, wood impregnation, etc., can solve problems such as polymerization inhibition, and achieve the effects of improving the preparation process, increasing the amount of impregnation, and good dimensional stability
- Summary
- Abstract
- Description
- Claims
- Application Information
AI Technical Summary
Problems solved by technology
Method used
Image
Examples
Embodiment 1
[0042] Take 200ml of MTES, 300ml of TEOS, and 100ml of water, put them into a flask and stir thoroughly, then add 10% hydrochloric acid to adjust the pH value to 1, then add 150ml of ethanol, gradually raise the temperature to 75°C, react for 60 minutes, then add ammonia water, The pH value was adjusted to 10, and the stirring reaction was continued for 30 minutes to obtain a transparent and clear sol, which was left at room temperature for later use.
[0043] Poplar wood after natural drying was taken as the wood to be treated, and a wood sample of 300×20×20mm was made. Put the sample into the processing tank of the processing system shown in Figure 1, start the vacuum pump to pump the pressure in the processing tank to 0.04MPa, and inhale the prepared in step 1 into the processing tank while keeping the vacuum state of the processing tank unchanged. Sol, make the wood sample completely immersed in the sol liquid, keep it for 30 minutes, open the inlet valve, release the vacu...
Embodiment 2
[0046] Take 350ml of MTES, 400ml of TEOS, and 90ml of water, put them into a flask and stir well, then add hydrochloric acid with a concentration of 6%, adjust the pH to 4, then add 100ml of ethanol, gradually raise the temperature to 80°C, and after 30 minutes of reaction, add ammonia water, The pH value was adjusted to 7, and the stirring reaction was continued for 40 minutes to obtain a transparent and clear sol, which was left at room temperature for later use.
[0047] Poplar wood after natural drying was taken as the wood to be treated, and a wood sample of 300×20×20mm was made. Put the sample into the processing tank of the processing system shown in Figure 1, start the vacuum pump to pump the pressure in the processing tank to 0.06MPa, and inhale the prepared in step 1 into the processing tank while keeping the vacuum state of the processing tank unchanged. Sol, make the wood sample completely immersed in the sol liquid, keep it for 60 minutes, open the inlet valve, re...
Embodiment 3
[0050] Take 400ml of MTES, 200ml of TEOS, and 50ml of water, put them into a flask and stir thoroughly, then add 1% hydrochloric acid to adjust the pH value to 6, then add 50ml of ethanol, gradually raise the temperature to 70°C, react for 90 minutes, then add ammonia water, The pH value was adjusted to 12, and the stirring reaction was continued for 20 minutes to obtain a transparent and clear sol, which was left at room temperature for later use.
[0051] Poplar wood after natural drying was taken as the wood to be treated, and a wood sample of 300×20×20mm was made. Put the sample into the processing tank of the processing system shown in Figure 1, start the vacuum pump to pump the pressure in the processing tank to 0.095MPa, and inhale the prepared in step 1 into the processing tank while keeping the vacuum state of the processing tank unchanged. Sol, make the wood sample completely immersed in the sol liquid, keep it for 90 minutes, open the inlet valve, release the vacuum...
PUM
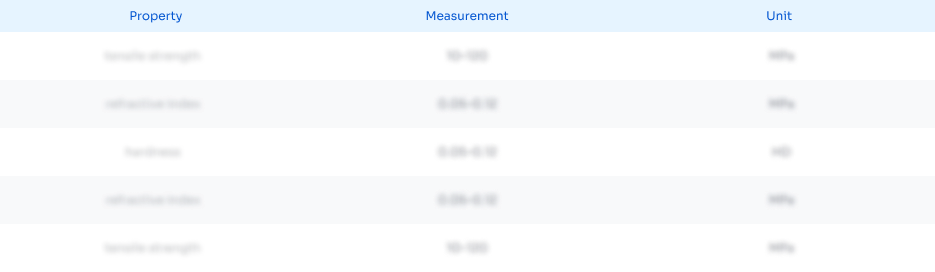
Abstract
Description
Claims
Application Information

- R&D
- Intellectual Property
- Life Sciences
- Materials
- Tech Scout
- Unparalleled Data Quality
- Higher Quality Content
- 60% Fewer Hallucinations
Browse by: Latest US Patents, China's latest patents, Technical Efficacy Thesaurus, Application Domain, Technology Topic, Popular Technical Reports.
© 2025 PatSnap. All rights reserved.Legal|Privacy policy|Modern Slavery Act Transparency Statement|Sitemap|About US| Contact US: help@patsnap.com