Novel rubber magnet and method for making same
A rubber magnet and system technology, applied in the direction of the magnetism of organic materials/organic magnetic materials, can solve the problems of rubber magnets that cannot be made into shapes, cannot be satisfied, and do not have the flexibility of rubber magnets.
- Summary
- Abstract
- Description
- Claims
- Application Information
AI Technical Summary
Problems solved by technology
Method used
Image
Examples
Embodiment 1
[0054] The proportion (mass ratio) of the magnet formula is 95% of quick-quenched NdFeB magnetic powder (brand: XQP16-10), 3% of nitrile rubber, 0.1% of coupling agent (such as KH-550), other additives such as lubricant, Plasticizers, vulcanizing agents, etc. accounted for 1.9%. The above raw materials are uniformly mixed in a mixing device such as a mixer, a high mixer, a screw mixer, an open mill, a calender or an internal mixer to obtain a billet. Fill the billet into a Φ50mm×Φ45×50mm mold and heat it to 150°C for 30 minutes, then shape it on a hydraulic press at a pressure of 5t / cm2, keep it warm at 150°C for 20 minutes, and demould it after cooling to obtain the final product. The detected magnet density is 5.7g / cm3, and the magnetic performance is 8.5MGO.
Embodiment 2
[0056] The proportion (mass ratio) of the magnet formula is 41% of quick-quenched NdFeB magnetic powder (brand: XQP16-10), 51% of strontium ferrite magnetic powder, 6% of nitrile rubber, 0.1% of coupling agent (such as KH-550), Other additives such as lubricants, plasticizers, vulcanizing agents, etc. accounted for 1.9%. The above raw materials are uniformly mixed in a mixing device such as a mixer, a high mixer, a screw mixer, an open mill, a calender or an internal mixer to obtain a billet. Fill the billet into a mold of Φ87mm×Φ81×2mm and heat it to 180°C for 20 minutes, then shape it on a vulcanizer under a pressure of 3t / cm2, and demould it after cooling to obtain the final product. The detected magnet density is 4.67g / cm3, and the magnetic property is 4.1MGO.
Embodiment 3
[0058] The proportion (mass ratio) of the magnet formula is HDDR anisotropic NdFeB magnetic powder (brand: 4013H) 95%, nitrile rubber 3%, coupling agent 0.1% (such as KH-550), other additives such as lubricants, Plasticizers, vulcanizing agents, etc. accounted for 1.9%. The above raw materials are uniformly mixed in a mixing device such as a mixer, a high mixer, a screw mixer, an open mill, a calender or an internal mixer to obtain pellets. Fill the pellets into a Φ20mm×3mm mold and heat it to 165°C for 20 minutes, then shape it on a hydraulic press with a pressure of 1t / cm2, and apply an axially oriented electromagnetic field of 2.8T at the same time, keep it at 150°C for 20 minutes, and after cooling Demoulding to obtain the final product. The detected magnet density is 5.7g / cm3, and the magnetic property is 13MGO.
[0059] Through the novel rubber magnet and its preparation method provided by the embodiments of the present invention, a novel rubber magnet is prepared, the...
PUM
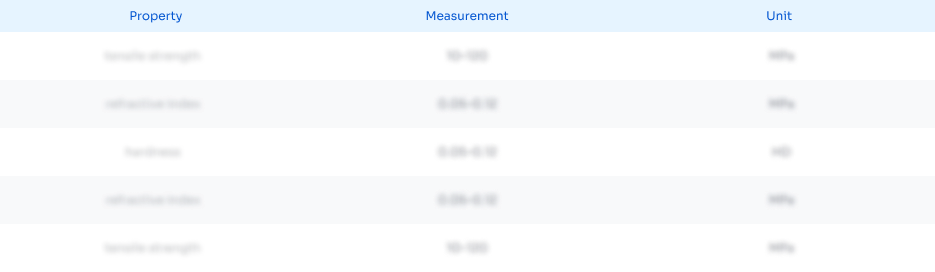
Abstract
Description
Claims
Application Information

- Generate Ideas
- Intellectual Property
- Life Sciences
- Materials
- Tech Scout
- Unparalleled Data Quality
- Higher Quality Content
- 60% Fewer Hallucinations
Browse by: Latest US Patents, China's latest patents, Technical Efficacy Thesaurus, Application Domain, Technology Topic, Popular Technical Reports.
© 2025 PatSnap. All rights reserved.Legal|Privacy policy|Modern Slavery Act Transparency Statement|Sitemap|About US| Contact US: help@patsnap.com