Method of manufacturing toothbrush with needle-shaped bristles, and toothbrush manufactured by the same
A manufacturing method, toothbrush technology, applied to the field of toothbrush, which will be embedded into the bristles of the toothbrush, to achieve the effect of enhanced machinability and high-efficiency embedding
- Summary
- Abstract
- Description
- Claims
- Application Information
AI Technical Summary
Problems solved by technology
Method used
Image
Examples
Embodiment 1
[0050] A bristle made of PBT having a thickness of 0.19 mm at the end was embedded in a mold mounted on a bristle fixation injection molding machine (model name: AFT CNC) manufactured by Boucherie, Belgium. Then, the part of the bristles protruding into the cavity of the mold is thermally welded, and resin is injected into the cavity of the mold to manufacture a toothbrush in which the bristles and the toothbrush body are integrated.
[0051] Subsequently, the bristles of the finished toothbrush are cut to a desired height with a finishing machine. Then, the bristles were partially tapered by a drum grinder having a raised portion so that the thickness at the tip of the bristles was 0.08 mm and the length of the tapered portion was 1.5 mm. The finished toothbrush was fixed on a holding jig, and then, the bristles were immersed in a reactor containing a 40% sodium hydroxide solution kept at 120° C. for 16 minutes. Subsequently, the bristles are washed in water, neutralized and...
Embodiment 2
[0054] Before the tapering process of the first embodiment, the bristles are cut so that the embedded bristles form the mountain shape shown in FIG. 3 .
[0055] The bristles on these toothbrushes were tapered in the same manner as in the first embodiment. As a result, the toothbrush bristles have a thickness ranging from 0.01 mm to 0.05 mm at the tip. The length of the tapered portion of the bristles ranges from 4mm to 8mm.
Embodiment 3
[0057] A bristle made of PBT having a thickness of 0.19 mm at the end was inserted into the fixing hole after being folded in half. At this time, 26 bristles are embedded in each fixing hole so that there is a height difference of 3 mm to 4 mm between the longer part and the shorter part of each bristle. After the bristle fixing treatment, the bristles were tapered so that the longer and shorter parts of the bristles had a thickness at the tip of 0.08 mm and a length of 1.5 mm at the tapered part. Thereafter, the bristles were tapered so that the longer portion of the bristles was slightly immersed in the chemical for 15 minutes. As a result, the end thickness of the longer portion of the bristles ranges from 0.01mm to 0.02mm. The length of the tapered portion of the longer portion ranges from 4mm to 7mm. The thickness of the shorter portion of the bristles was maintained at 0.08mm at the end.
PUM
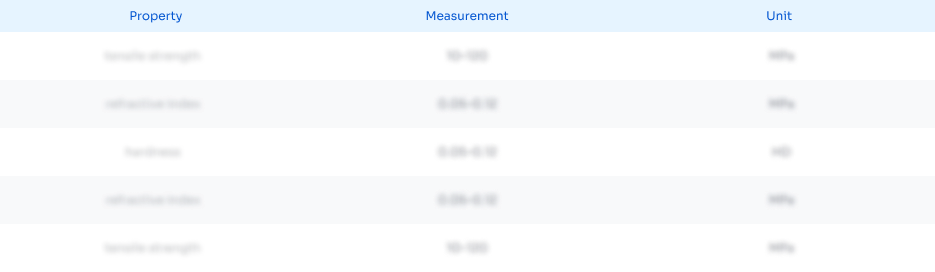
Abstract
Description
Claims
Application Information

- R&D Engineer
- R&D Manager
- IP Professional
- Industry Leading Data Capabilities
- Powerful AI technology
- Patent DNA Extraction
Browse by: Latest US Patents, China's latest patents, Technical Efficacy Thesaurus, Application Domain, Technology Topic, Popular Technical Reports.
© 2024 PatSnap. All rights reserved.Legal|Privacy policy|Modern Slavery Act Transparency Statement|Sitemap|About US| Contact US: help@patsnap.com