Multiple hanging points crane electric control method
An electrical control and crane technology, applied in the direction of load hanging components, transportation and packaging, can solve the problems of unstable operation of the system, hidden dangers, and complexity of the system, and achieve significant economic and social benefits.
- Summary
- Abstract
- Description
- Claims
- Application Information
AI Technical Summary
Problems solved by technology
Method used
Image
Examples
Embodiment Construction
[0027] As shown in Figure 4, the super large tonnage multi-lifting point crane provided by the present invention needs to adopt a special mechanical structure in order to meet the special process requirements of the overall lifting of drilling platforms and other large non-uniform loads, that is, the hoisting mechanism is composed of multiple sets of hoisting systems. Among them, there are as many as 24 hoisting points 9 on the main beam 11, driven by 6 hoisting systems 10. Therefore, the crane's control system is important to complete the hoisting safely and smoothly. The electrical system of the super large tonnage multi-lifting point crane consists of high and low voltage power supply and distribution system; lifting mechanism drive control system; PLC control and management system; signal detection and safety protection system; auxiliary systems such as lighting, signal, ventilation and heating; fire protection, industrial TV monitoring system; communication system, lightning ...
PUM
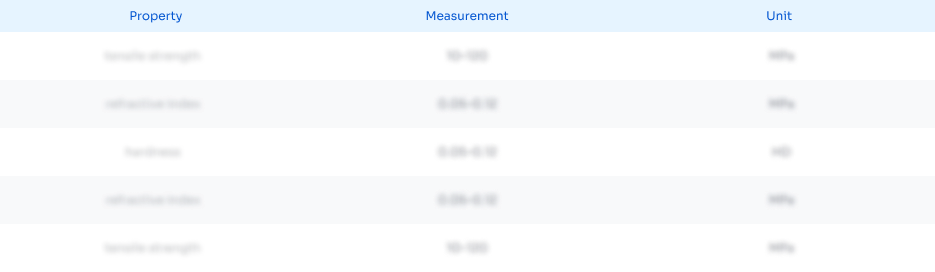
Abstract
Description
Claims
Application Information

- R&D
- Intellectual Property
- Life Sciences
- Materials
- Tech Scout
- Unparalleled Data Quality
- Higher Quality Content
- 60% Fewer Hallucinations
Browse by: Latest US Patents, China's latest patents, Technical Efficacy Thesaurus, Application Domain, Technology Topic, Popular Technical Reports.
© 2025 PatSnap. All rights reserved.Legal|Privacy policy|Modern Slavery Act Transparency Statement|Sitemap|About US| Contact US: help@patsnap.com