Die-casting mould and preparation method of die-casting product thereof
A technology for die-casting molds and products, which is applied in the production of die-casting molds and die-casting products. It can solve the problems of peeling off of the heating body plate and the pressure welding strength cannot withstand the thermal cycle work load, etc., so as to improve the damage resistance and simplify the production process. , the effect of expanding the scope of use
- Summary
- Abstract
- Description
- Claims
- Application Information
AI Technical Summary
Problems solved by technology
Method used
Image
Examples
Embodiment Construction
[0018] The present invention is described in further detail below in conjunction with accompanying drawing (embodiment):
[0019] With reference to accompanying drawing 1-3, the present invention is made of mold base 1, rear mold meat 2, front mold meat 3, heater plate 4, electromagnet coil 5, bolt 6, electromagnet core 7, non-electromagnet steel ring 8, Date type pin 9, type hole type pin 10, rear mold insert 11, support column 12, hoisting hole type pin 13, point cooling water channel 14, ejector plate guide post 15, vacuum valve 16, air cooling channel 17, pin 18 , sprue sleeve 19, diverter cone 20, and electromagnetic pot mold 21. Set the front mold meat 3 and the rear mold meat 2 in the mold base 1, set the support column 12 at the bottom of the mold base 1, and set it in the front mold meat 3. Electromagnetic pot mold 21, on electromagnetic pot mold 21 heating body plate 4 is set, and its interval is 3 millimeters, electromagnet iron core 7 is set on heating body plate 4...
PUM
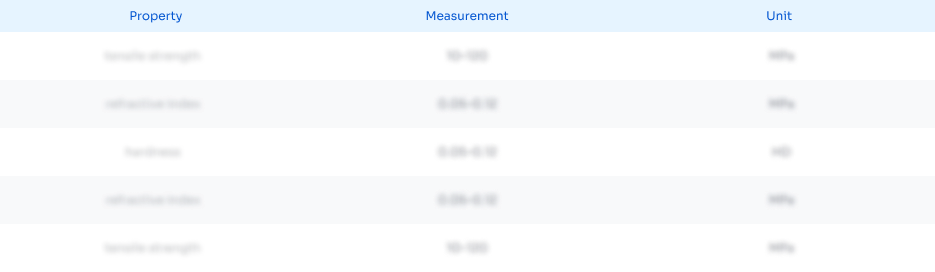
Abstract
Description
Claims
Application Information

- R&D Engineer
- R&D Manager
- IP Professional
- Industry Leading Data Capabilities
- Powerful AI technology
- Patent DNA Extraction
Browse by: Latest US Patents, China's latest patents, Technical Efficacy Thesaurus, Application Domain, Technology Topic, Popular Technical Reports.
© 2024 PatSnap. All rights reserved.Legal|Privacy policy|Modern Slavery Act Transparency Statement|Sitemap|About US| Contact US: help@patsnap.com