Method for producing concrete active admixture by iron tailings
A technology of active admixture and iron tailings, applied in the direction of climate sustainability, sustainable waste treatment, solid waste management, etc. Grade concrete and other problems to achieve the effect of alleviating the shortage of ultra-fine slag powder, increasing the dosage, reducing energy consumption and environmental pollution
- Summary
- Abstract
- Description
- Claims
- Application Information
AI Technical Summary
Problems solved by technology
Method used
Examples
Embodiment 1
[0011] 90% of magnetite-quartzite-type iron tailings, 3% of lime, 4% of dihydrate gypsum, and 3% of altering agent are dry-mixed and ground to a fineness of 80 μm and sieved to 2.5%, and then the mixed and ground materials are The hydrothermal alteration reaction is carried out at 700°C in a cyclone suspension reactor, and the reaction time is 10 seconds. After cooling the above-mentioned reacted product, the obtained material is 80% by weight, and then mixed with 20% slag powder and ground to a fineness of 80 μm, and the remaining 0.3% of the sieve is obtained to obtain a concrete admixture that can replace slag superfine powder. . All performance indexes of the active admixture meet the performance indexes specified in S95 in GB / T18046-2000 "Granulated Blast Furnace Slag Powder Used in Cement and Concrete".
Embodiment 2
[0013] 80% of magnetite-quartzite-type iron tailings, 15% of lime, 3% of dihydrate gypsum, and 2% of alteration agent are dry-blended and ground to a fineness of 80 μm and sieved to 2.5%, and then the mixed-milled materials are The hydrothermal alteration reaction is carried out at 700°C in the cyclone suspension reactor, and the reaction time is 7 seconds. After cooling the above-mentioned reacted product, the obtained material is 40% by weight, and then mixed with 60% slag powder and ground to a fineness of 80 μm, and the remaining 0.3% of the sieve is obtained to obtain a concrete admixture that can replace slag superfine powder. . All performance indexes of the active admixture meet the performance indexes specified in S105 in GB / T18046-2000 "Granulated Blast Furnace Slag Powder Used in Cement and Concrete".
Embodiment 3
[0015] 85% of magnetite-quartzite-type iron tailings, 11.8% of calcium carbide slag, 3% of desulfurized gypsum, and 0.2% of altering agent are wet-mixed and ground to a fineness of 1% after the sieve residue of 80 μm, and then press-filtered and dehydrated. The materials are made into bricks and reacted in a tunnel kiln. The temperature of the firing zone in the kiln is controlled at 700°C±30°C, and the reaction time in the firing zone is 7 hours.
[0016] The material obtained after cooling the above-mentioned altered product is mixed with 10% slag at a weight percentage of 90% and ground until the sieve residue of 80 μm is 0.3%. The active concrete admixture that can be used instead of slag superfine powder is obtained. All performance indexes of the active admixture meet the performance indexes specified in S95 in GB / T18046-2000 "Granulated Blast Furnace Slag Powder Used in Cement and Concrete".
PUM
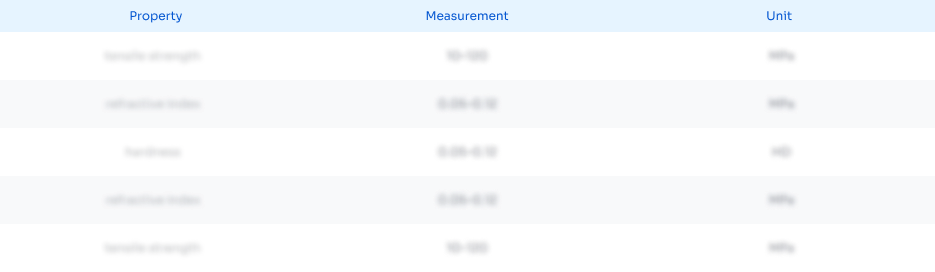
Abstract
Description
Claims
Application Information

- Generate Ideas
- Intellectual Property
- Life Sciences
- Materials
- Tech Scout
- Unparalleled Data Quality
- Higher Quality Content
- 60% Fewer Hallucinations
Browse by: Latest US Patents, China's latest patents, Technical Efficacy Thesaurus, Application Domain, Technology Topic, Popular Technical Reports.
© 2025 PatSnap. All rights reserved.Legal|Privacy policy|Modern Slavery Act Transparency Statement|Sitemap|About US| Contact US: help@patsnap.com