Machine system with a thermo-syphon cooled superconductor rotor winding
A technology of rotor windings and machines, applied in the usage of superconductor elements, regenerative heat exchangers, cooling/ventilation devices, etc., can solve problems such as large heat loss, inability to meet the service life requirements of the shipbuilding industry, and achieve good The effect of thermally conductive coupling
- Summary
- Abstract
- Description
- Claims
- Application Information
AI Technical Summary
Problems solved by technology
Method used
Image
Examples
Embodiment Construction
[0029] The machine system of the present invention includes a machine or an electric motor, and also includes an auxiliary cooling unit. In the embodiments described below with the aid of the figures, this machine can in particular be a synchronous motor or a generator. The machine comprises a rotating superconducting winding which can in principle be made of metallic LTS material or oxidized HTS material. The second material is preferably used in the following examples. The winding can be formed with a coil or a coil system in a 2-pole, 4-pole or other multi-pole arrangement by means of corresponding conductors. The drawing shows the basic structure of a corresponding synchronous motor, the machine system being of the embodiment disclosed in WO 02 / 15370 A1 mentioned at the outset ( FIG. 5 , in conjunction with FIGS. 2 and 3 ).
[0030] The machine indicated at 2 comprises a stationary outer casing 3 at room temperature with a stator winding 4 . A rotor 5 is surrounded by t...
PUM
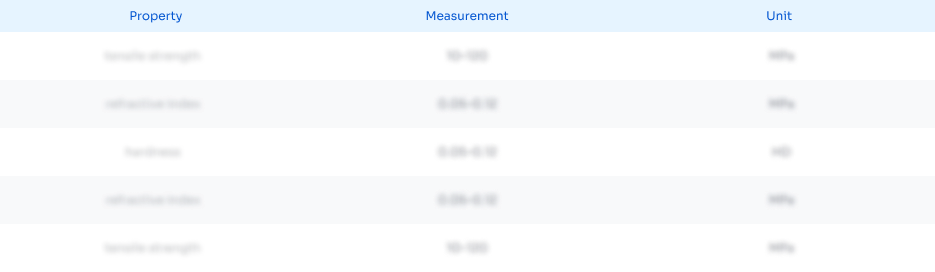
Abstract
Description
Claims
Application Information

- R&D
- Intellectual Property
- Life Sciences
- Materials
- Tech Scout
- Unparalleled Data Quality
- Higher Quality Content
- 60% Fewer Hallucinations
Browse by: Latest US Patents, China's latest patents, Technical Efficacy Thesaurus, Application Domain, Technology Topic, Popular Technical Reports.
© 2025 PatSnap. All rights reserved.Legal|Privacy policy|Modern Slavery Act Transparency Statement|Sitemap|About US| Contact US: help@patsnap.com