Method for manufacturing paper stuff with cassava root material
A manufacturing method and pulp technology, which can be applied in the fields of cellulose raw material pulping, papermaking, non-woody plant/crop pulp, etc., can solve the problems of time-consuming collection and high price, and achieve easy search, better paper quality, and lower cost. cost effect
- Summary
- Abstract
- Description
- Claims
- Application Information
AI Technical Summary
Problems solved by technology
Method used
Image
Examples
Embodiment Construction
[0050] Please refer to Fig. 1, the present invention proposes a kind of manufacturing method that cassava root material makes paper pulp, and it comprises the following steps:
[0051] Step 1, HD (hydra pulper) step: mix the raw material with water, the raw material is cassava root, keep its concentration and proportion at about 4-10%, the above ratio is the weight ratio, and then enter the next step;
[0052] Step 2. HC (high consistency cleaner) separation step: separate the impurities whose specific gravity is greater than that of pulp, such as sand, stone and others, and separate them with a concentration of 4-10% before proceeding to the next step;
[0053] Step 3, FF (fiber fretter) step: separating the pulp, distinguishing the long-fiber pulp and the short-fiber pulp, and then respectively entering the next step with the separated long- and short-fiber pulp;
[0054] Afterwards, the long and short fiber pulp will be separated into the respective steps:
[0055] Wherein...
PUM
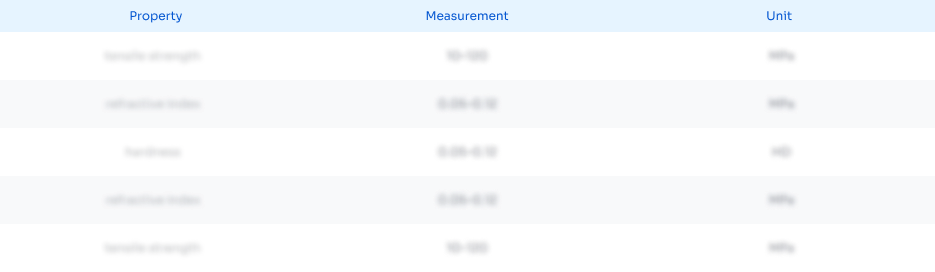
Abstract
Description
Claims
Application Information

- R&D Engineer
- R&D Manager
- IP Professional
- Industry Leading Data Capabilities
- Powerful AI technology
- Patent DNA Extraction
Browse by: Latest US Patents, China's latest patents, Technical Efficacy Thesaurus, Application Domain, Technology Topic, Popular Technical Reports.
© 2024 PatSnap. All rights reserved.Legal|Privacy policy|Modern Slavery Act Transparency Statement|Sitemap|About US| Contact US: help@patsnap.com