Reluctance motor
A reluctance motor and motor technology, which is applied to electric components, magnetic circuit rotating parts, electromechanical devices, etc., can solve the problems of low power per unit volume of motors, torque ripple of reluctance motors, complex control systems, etc., and achieve cost reduction. , to achieve frequency self-sufficiency and positioning control, the effect of simple control system
- Summary
- Abstract
- Description
- Claims
- Application Information
AI Technical Summary
Problems solved by technology
Method used
Image
Examples
Embodiment Construction
[0040] according to figure 1 As mentioned above, the reluctance motor of the present invention adopts a three-phase stator structure, that is, six stator poles are distributed equidistantly on the circumference, and the width of each stator pole is equal to the spacing. A simple concentrated winding is installed on each stator pole, and the windings on the two radially opposite stator poles are connected in series or in parallel to form a phase. That is: the L 1 and L 4 Form A phase, L 2 and L 5 Form B phase, L 3 and L 6 To form the C phase, the magnetic flux polarity between the adjacent stator poles should be designed to be opposite to each other. Then, the elliptical two-pole rotor core 4 is installed on the hollow rotor shaft 5, and passed through the two ends of the motor. Bearings, end caps (not shown in the figure) are connected and fixed with the machine base 1. The motion mechanism that constitutes the entire motor. Among them, at both ends of the long axis of...
PUM
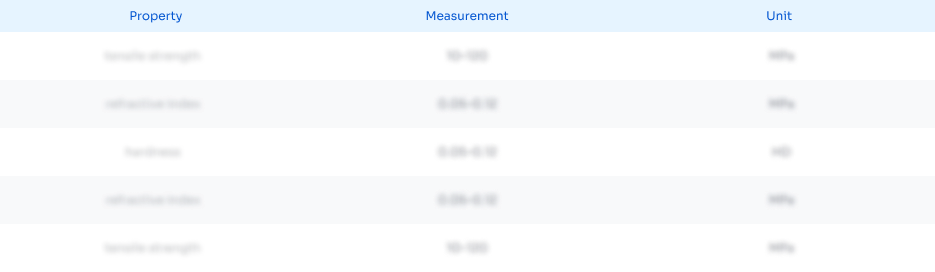
Abstract
Description
Claims
Application Information

- R&D
- Intellectual Property
- Life Sciences
- Materials
- Tech Scout
- Unparalleled Data Quality
- Higher Quality Content
- 60% Fewer Hallucinations
Browse by: Latest US Patents, China's latest patents, Technical Efficacy Thesaurus, Application Domain, Technology Topic, Popular Technical Reports.
© 2025 PatSnap. All rights reserved.Legal|Privacy policy|Modern Slavery Act Transparency Statement|Sitemap|About US| Contact US: help@patsnap.com