Method for realizing numerical control rotating platform angular displacement forecast measurement using time gate displacement sensor
A technology of displacement sensor and time grating, which is applied in the direction of using electric/magnetic devices to transmit sensing components, digital control, electrical program control, etc., and can solve the problem that the time grating cannot be applied to dynamic continuous position feedback.
- Summary
- Abstract
- Description
- Claims
- Application Information
AI Technical Summary
Problems solved by technology
Method used
Image
Examples
Embodiment Construction
[0021] Below in conjunction with concrete hardware and software illustrate the realization of the inventive method:
[0022] Referring to Figure 4, the time grid uses a digital signal processor DSP (U1) to process data, and its specific model is TMS320VC33. The / STRB and PAGE3 terminals of U1 pass through the OR gate U31, the output terminal of U31 is connected to one input terminal of the NOR gate U32, the other input terminal of U32 is connected to the AO terminal of U1, and the output terminal of U32 is connected to U1 in two ways The EINT3 end and the LOCK end of the latch U33. The 32 data input lines D31~D0 of U33 are connected with the 32 data lines D31~D0 of U1 in turn, and the 32 data output lines O31~O0 of U33 are respectively connected with two 16-bit tri-state bus buffers (U34 and U35). The data input lines D15-D0 are connected, and the data output lines O15-O0 of U34 and U35 are all connected to the P0.17-P0.2 terminals of the ARM processor LPC2138 (U2). The outp...
PUM
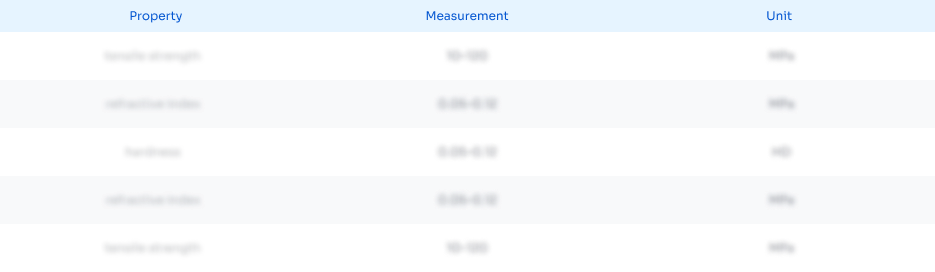
Abstract
Description
Claims
Application Information

- R&D
- Intellectual Property
- Life Sciences
- Materials
- Tech Scout
- Unparalleled Data Quality
- Higher Quality Content
- 60% Fewer Hallucinations
Browse by: Latest US Patents, China's latest patents, Technical Efficacy Thesaurus, Application Domain, Technology Topic, Popular Technical Reports.
© 2025 PatSnap. All rights reserved.Legal|Privacy policy|Modern Slavery Act Transparency Statement|Sitemap|About US| Contact US: help@patsnap.com