Electrically driven linear actuator
A linear actuator and electric drive technology, applied in the direction of electric components, electromechanical devices, electrical components, etc., can solve the problems of distorted target moving distance, distorted results, fatigue of elastic intermediate members, etc., and achieve high reliability and operational safety , the effect of high actuation precision
- Summary
- Abstract
- Description
- Claims
- Application Information
AI Technical Summary
Problems solved by technology
Method used
Image
Examples
Embodiment Construction
[0027] As shown in Figure 1, the linear actuator of the present invention comprises a sleeve 18, which has a sleeve bottom 19 disposed at one end thereof, and a sleeve head 20 disposed at its other end; transmission 11 to the casing bottom 19; and an electric motor 10 for driving by the transmission 11; a spindle 24 mounted coaxially inside the casing 18 and through a transmission-side bearing 22 And the output side bearing 23 is installed in a rotatable manner. A spindle nut 21 engaged with the external thread of the spindle 24 is inserted on the spindle 24 . The spindle nut 21 is held inside a piston 25 mounted to slide on the inner surface of the sleeve 18 and is coupled via the piston 25 to an outer cylinder or actuator tube 31 which communicates with an inner cylinder or actuator tube 31 . The actuator tube 32 and the elastic material layer 33 frictionally connecting the two actuator tubes 31 and 32 together form a hollow cylindrical actuator element. The outer actuator...
PUM
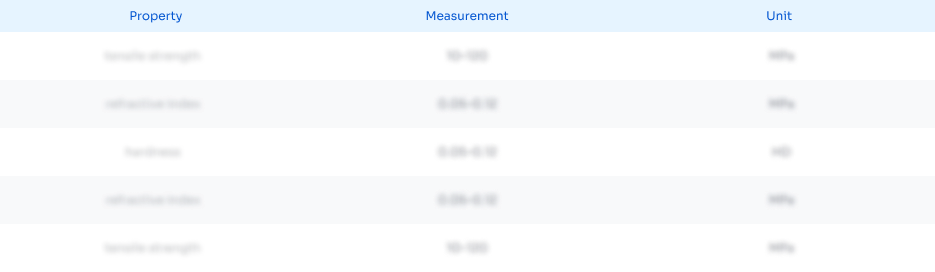
Abstract
Description
Claims
Application Information

- R&D
- Intellectual Property
- Life Sciences
- Materials
- Tech Scout
- Unparalleled Data Quality
- Higher Quality Content
- 60% Fewer Hallucinations
Browse by: Latest US Patents, China's latest patents, Technical Efficacy Thesaurus, Application Domain, Technology Topic, Popular Technical Reports.
© 2025 PatSnap. All rights reserved.Legal|Privacy policy|Modern Slavery Act Transparency Statement|Sitemap|About US| Contact US: help@patsnap.com