Thread winding device and assembling method thereof
A winding device and assembly method technology, which is applied in coil manufacturing and other directions, can solve problems such as increased stray capacitance, easy disconnection of lead wires, and increased working hours, so as to reduce leakage magnetic flux and noise, and improve insulation withstand voltage , Reduce the effect of leakage flux
- Summary
- Abstract
- Description
- Claims
- Application Information
AI Technical Summary
Problems solved by technology
Method used
Image
Examples
Embodiment Construction
[0026] Hereinafter, an embodiment in which the winding device of the present invention is applied to a transformer for high voltage will be described with reference to FIGS. 1 to 6 . In FIGS. 1 to 6 , the parts that are substantially the same as those shown in FIGS. 7 and 8 are denoted by the same reference numerals, and description thereof will be omitted.
[0027] As shown in Figures 1 to 3, the transformer of this embodiment has a first bobbin (31), a second bobbin (32) and a pair of E-shaped cores (11, 12) as cores, the first winding The bobbin (31) has a cavity (31d) and the coil (21) for high voltage is wound on the outside; the second bobbin (32) is assembled in a manner surrounding the first bobbin (31) and the coil for low voltage ( 22) The package is on the outside; a pair of E-shaped cores (11, 12) are installed in the cavity (31d) of the first bobbin (31) and the outside of the second bobbin (32) to form a closed magnetic circuit. The first bobbin (31) has a cylin...
PUM
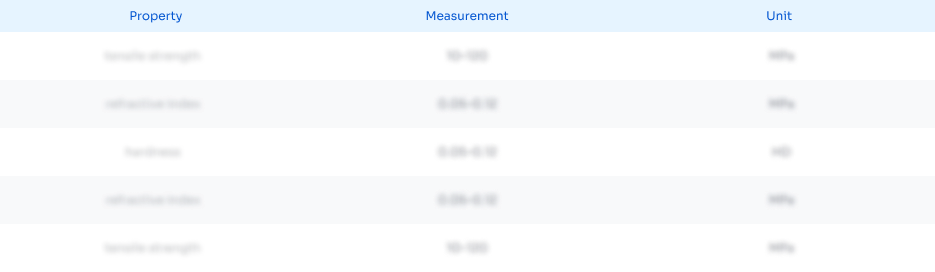
Abstract
Description
Claims
Application Information

- R&D Engineer
- R&D Manager
- IP Professional
- Industry Leading Data Capabilities
- Powerful AI technology
- Patent DNA Extraction
Browse by: Latest US Patents, China's latest patents, Technical Efficacy Thesaurus, Application Domain, Technology Topic, Popular Technical Reports.
© 2024 PatSnap. All rights reserved.Legal|Privacy policy|Modern Slavery Act Transparency Statement|Sitemap|About US| Contact US: help@patsnap.com