A package method for double-side silicon-glass solar cell assembly
A solar cell module and double-sided glass technology, which is applied in the direction of electrical components, semiconductor devices, circuits, etc., can solve the problem that the yield rate of the product is competitive with ordinary components, the high process cost is not suitable for large-scale production, and the packaging process has technical bottlenecks and other problems, to achieve the effect of avoiding cell fragments, strong impact resistance, and optimizing the lamination process
- Summary
- Abstract
- Description
- Claims
- Application Information
AI Technical Summary
Problems solved by technology
Method used
Image
Examples
Embodiment 1
[0019] As shown in Figure 1, first lay a piece of low-iron tempered glass 3 on the table, and spread a single layer of EVA film 2 with a thickness of 0.3mm on it, and put the series and parallel solar cell strings 1 on the EVA film. 2 Above, a single layer of EVA film 2 with a thickness of 0.3mm and low-iron tempered glass 3 are also laid on the solar cell string 1 to form a 5-layer structure of 3-2-1-2-3; Then use polymer materials to perform specific treatment on the above five-layer structure; then set the preheating temperature of the laminator to 70℃, when the temperature of the heating plate of the laminator reaches this temperature, put the above-mentioned processed five-layer structure into In the laminator, the upper cover of the laminator is combined, and the lower chamber of the laminator is evacuated while the upper chamber is inflated to pressurize the laminated battery; the laminating temperature of the laminator is set to 140℃, The lamination time at temperature is ...
Embodiment 2
[0021] As shown in Figure 1, first lay a piece of low-iron tempered glass 3 on the table, and lay a single layer of EVA film 2 with a thickness of 0.3mm on it, and put the series and parallel solar cell strings 1 on the EVA film 2. Above, two layers of EVA film 2 with a thickness of 0.3mm and low-iron tempered glass 3 are also sequentially stacked on the solar cell string 1 to form a 5-layer structure of 3-2-1-2-3; Use polymer materials to perform specific treatment on the above five-layer structure; then set the preheating temperature of the laminator to 70℃, when the temperature of the heating plate of the laminator reaches this temperature, put the above-treated five-layer structure into the layer In the press, the upper cover of the laminator is combined, and the lower chamber of the laminator is evacuated while the upper chamber is inflated to pressurize the laminated battery; the laminating temperature of the laminator is set to 140 ℃, at this temperature The lower laminatio...
Embodiment 3
[0023] As shown in Figure 1, first lay a piece of low-iron tempered glass 3 on the table, and spread a single layer of EVA film 2 with a thickness of 0.3mm on it, and put the series and parallel solar cell strings 1 on the EVA film. 2 Above, three layers of EVA film 2 with a thickness of 0.3mm and low-iron tempered glass 3 are also sequentially stacked on the solar cell string 1 to form a 5-layer structure of 3-2-1-2-3; Then use polymer materials to perform specific treatment on the above five-layer structure; then set the preheating temperature of the laminator to 70℃, when the temperature of the heating plate of the laminator reaches this temperature, put the above-processed five-layer structure into In the laminator, the upper cover of the laminator is combined, and the lower chamber of the laminator is evacuated while the upper chamber is inflated to pressurize the laminated battery; the laminating temperature of the laminator is set to 140°C. The lamination time at temperatur...
PUM
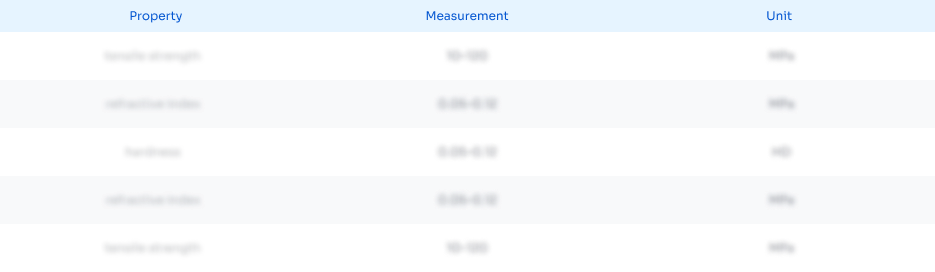
Abstract
Description
Claims
Application Information

- Generate Ideas
- Intellectual Property
- Life Sciences
- Materials
- Tech Scout
- Unparalleled Data Quality
- Higher Quality Content
- 60% Fewer Hallucinations
Browse by: Latest US Patents, China's latest patents, Technical Efficacy Thesaurus, Application Domain, Technology Topic, Popular Technical Reports.
© 2025 PatSnap. All rights reserved.Legal|Privacy policy|Modern Slavery Act Transparency Statement|Sitemap|About US| Contact US: help@patsnap.com