Low power consumption axial magnetic bearing with redundant structure
A technology of axial magnetic bearing and redundant structure, applied in the direction of shaft and bearing, bearing, mechanical equipment, etc., can solve the problems of low reliability and high power consumption, and achieve the purpose of increasing the magnetic pole area, improving the bearing capacity and simple structure. Effect
- Summary
- Abstract
- Description
- Claims
- Application Information
AI Technical Summary
Problems solved by technology
Method used
Image
Examples
Embodiment Construction
[0017] As shown in Fig. 2, Fig. 3 and Fig. 4, it is a low-power axial magnetic bearing with redundant structure, which is one of the technical solutions of the present invention, which is the basic form of the present invention. It consists of bearing body 9, excitation coils 2 and 3, permanent magnet 4, magnetic conduction ring 5, air gap 7, auxiliary air gap 10 and suspension body 6, permanent magnet 4 is closely attached to bearing body 9, magnetic conduction ring 5 It is closely attached to the permanent magnet 4 and forms an auxiliary air gap 10 with the bearing body 9 in the axial direction. The bearing body 9 includes an outer magnetic pole 91 and a middle magnetic pole 92. An air gap 7 is formed between them, and the permanent magnet 4 generates a bias magnetic flux in the air gap 7. Two sets of excitation coils 2 and 3 are wound in the bearing body 9, and the excitation coils 2 and 3 are used to generate control magnetic flux. The excitation coils 2, The permanent mag...
PUM
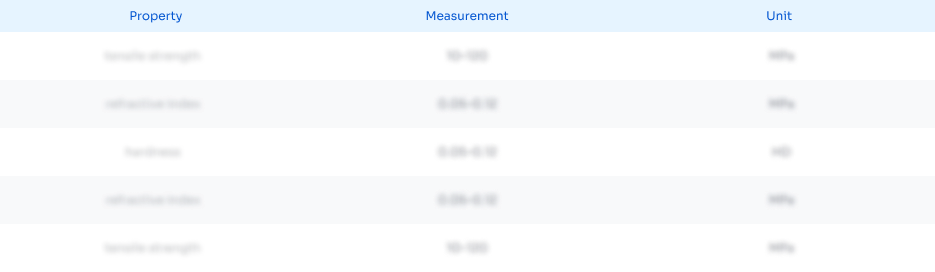
Abstract
Description
Claims
Application Information

- Generate Ideas
- Intellectual Property
- Life Sciences
- Materials
- Tech Scout
- Unparalleled Data Quality
- Higher Quality Content
- 60% Fewer Hallucinations
Browse by: Latest US Patents, China's latest patents, Technical Efficacy Thesaurus, Application Domain, Technology Topic, Popular Technical Reports.
© 2025 PatSnap. All rights reserved.Legal|Privacy policy|Modern Slavery Act Transparency Statement|Sitemap|About US| Contact US: help@patsnap.com