Method of preparing composite material of silicon nitride and silicon carbide by reverse reaction sintering
A technology of silicon nitride, silicon carbide, and composite materials, which is applied in the field of inorganic non-metallic material science and engineering, can solve the problems of inconvenient production by the nitriding method, and achieve the effects of large-scale production, high performance, and simple equipment
- Summary
- Abstract
- Description
- Claims
- Application Information
AI Technical Summary
Problems solved by technology
Method used
Examples
example 1
[0014] 1. Ingredients: SiC: the particle size is 2.8mm sieve material and 0.9mm sieve material, the mass fraction ratio is 35%; SiC: the particle size is 0.9mm sieve material and 0.15mm sieve material, the mass fraction ratio is 30% %; SiC: undersize with a particle size of 0.115mm, the mass fraction ratio is 5%; SiC: undersize with a particle size of 0.045mm, with a mass fraction ratio of 4%; SiC with a particle size of over 0.004mm undersize, with a mass fraction ratio of 5%; silicon nitride (Si 3 N 4 ): the particle size is 0.074mm sieve material, the mass fraction ratio is 21%; the external resin mass ratio is 5%,
[0015] 2. Forming: Forming by vibration method, put the prepared mud into the steel mold on the vibration table, the vibration frequency of the vibration platform is 50 Hz, the amplitude is 0.1 mm, and the forming load is 8kPa.
[0016] 3. Drying: heat preservation at 150°C for 24hrs
[0017] 4. Firing: Firing in air atmosphere, firing heating curve:
[001...
example 2
[0023] 1. Ingredients: SiC: the particle size is 2.8mm sieve material and 0.9mm sieve material, the mass fraction ratio is 35%; SiC: the particle size is 0.9mm sieve material and 0.15mm sieve material, the mass fraction ratio is 30% %; SiC: undersize with a particle size of 0.115mm, the mass fraction ratio is 5%; SiC: undersize with a particle size of 0.045mm, with a mass fraction ratio of 5%; SiC with a particle size over 0.004mm undersize, with a mass fraction ratio of 5%; metal silicon, the particle size is 180 mesh sieve, and the mass fraction ratio is 3%; silicon nitride (Si 3 N 4 ): the particle size is 0.074mm undersize, and the mass fraction ratio is 17%; the mass ratio of resin is 7%.
[0024] 2. Forming: Forming by vibration method, put the prepared mud into the steel mold on the vibration table, the vibration frequency of the vibration platform is 50 Hz, the amplitude is 0.1 mm, and the forming load is 8kPa. The density of semi-finished products is controlled at 2...
example 3
[0032] 1. Ingredients: SiC: the particle size is 2.8mm sieve material and 0.9mm sieve material, the mass fraction ratio is 35%; SiC: the particle size is 0.9mm sieve material and 0.15mm sieve material, the mass fraction ratio is 30% %; SiC: the particle size is 0.115mm sieve material, the mass fraction ratio is 5%; metal silicon, the particle size is 180 mesh sieve material, the mass fraction ratio is 5%; silicon nitride (Si 3 N 4 ): the particle size is 0.074mm sieve material, the mass fraction ratio is 20%; silicon nitride (Si 3 N 4 ): the particle size is 0.004mm undersize, and the mass fraction ratio is 5%; the mass ratio of resin is 5%.
[0033] 2. Forming: Forming by vibration method, put the prepared mud into the steel mold on the vibration table, the vibration frequency of the vibration platform is 50 Hz, the amplitude is 0.1 mm, and the forming load is 8kPa.
[0034] 3. Drying: heat preservation at 150°C for 24hrs
[0035] 4. Firing: Firing in air atmosphere, firi...
PUM
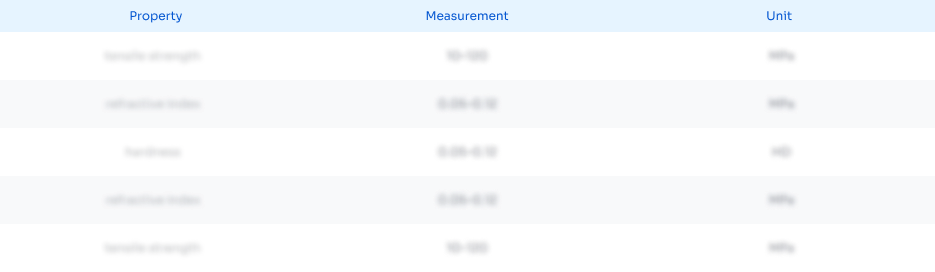
Abstract
Description
Claims
Application Information

- R&D Engineer
- R&D Manager
- IP Professional
- Industry Leading Data Capabilities
- Powerful AI technology
- Patent DNA Extraction
Browse by: Latest US Patents, China's latest patents, Technical Efficacy Thesaurus, Application Domain, Technology Topic, Popular Technical Reports.
© 2024 PatSnap. All rights reserved.Legal|Privacy policy|Modern Slavery Act Transparency Statement|Sitemap|About US| Contact US: help@patsnap.com