Sputter chamber for coating a substrate
A sputtering chamber and substrate technology, applied in the field of sputtering chambers, can solve the problems of substrate layer thickness fluctuation, large loss, and different coating rates
- Summary
- Abstract
- Description
- Claims
- Application Information
AI Technical Summary
Problems solved by technology
Method used
Image
Examples
Embodiment Construction
[0024] FIG. 1 shows a section through a sputtering chamber 1 with a cathode space 2 and two adjacent pumping spaces 3, 4 each equipped with preferably Pumps 5, 6 of turbo pumps. Auxiliary pumping chambers 9 , 10 are arranged below these pumping spaces 3 , 4 , and the substrate space 7 is located between the auxiliary pumping chambers 9 , 10 .
[0025] In the substrate space 7, a substrate 8, which may be a glass sheet, is conveyed from left to right on rollers 11, 12, 30. The pumping spaces 3 , 4 are connected via openings 13 to 16 to the substrate space 7 , the cathode space 2 or the auxiliary pumping chambers 9 , 10 .
[0026] The cathode 19 is arranged on a cover 17 which is placed on the sputtering chamber 1 via a mount 18 , and the target 2 is fastened on the cathode 19 . An anode 21 in the form of a hole is arranged opposite the cathode 19 . Arranged on the cover 17 is a cathode cap 22 comprising a cooling system 23 in which preferably water flows as coolant.
[0027...
PUM
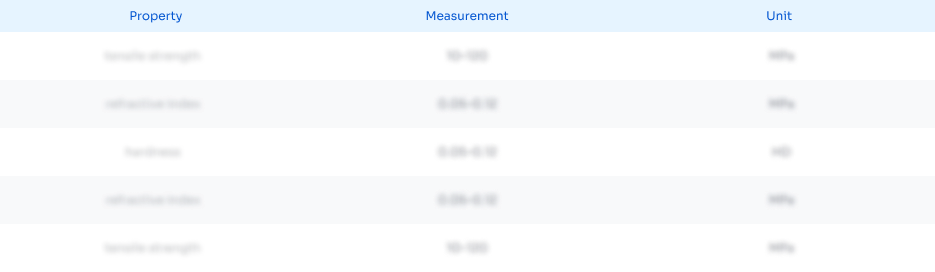
Abstract
Description
Claims
Application Information

- R&D Engineer
- R&D Manager
- IP Professional
- Industry Leading Data Capabilities
- Powerful AI technology
- Patent DNA Extraction
Browse by: Latest US Patents, China's latest patents, Technical Efficacy Thesaurus, Application Domain, Technology Topic, Popular Technical Reports.
© 2024 PatSnap. All rights reserved.Legal|Privacy policy|Modern Slavery Act Transparency Statement|Sitemap|About US| Contact US: help@patsnap.com