Numerical-control machine tool magnetic suspension linear feeding system
A linear feed system, CNC machine tool technology, applied in the direction of the propulsion system, control/regulation system, electromechanical devices, etc., can solve the problems of poor stiffness performance, poor bearing capacity, instability, etc., to achieve improved bearing capacity and good stiffness performance , the effect of improving efficiency
- Summary
- Abstract
- Description
- Claims
- Application Information
AI Technical Summary
Problems solved by technology
Method used
Image
Examples
Embodiment Construction
[0026] First, referring to accompanying drawings 1, 2, and 3, the maglev linear feed system for a numerically controlled machine tool of the present invention includes a base 1, two guide rails 14 fixed on the base 1, linear motor stator components 17, 18, installed in the working Four sets of differential levitation electromagnets 4 and 10 below the four corners of platform 5, two sets of guide electromagnets 11 installed next to the levitation electromagnet 10, and two sets of guide electromagnets 11 installed next to the levitation electromagnets 4, 10 and guide electromagnet 11 Eddy current displacement sensors 19, 21, linear motor mover components 8, 15, 16 installed under the workbench 5, grating scale 6 installed on the guide rail, grating reading head 7 installed under the workbench, installed under the workbench The supporting device 9 and the guide rail protective cover (not shown in the figure).
[0027]A working cycle of the present invention will be described in d...
PUM
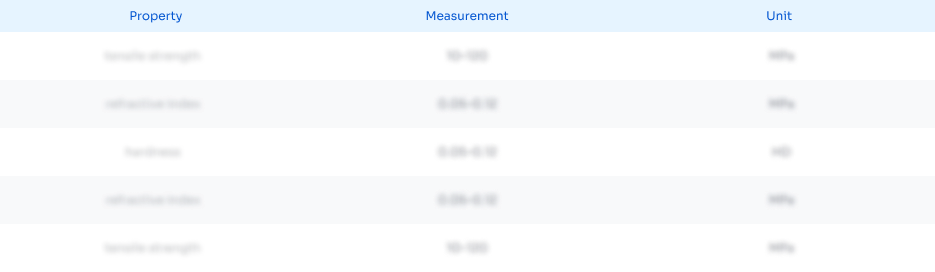
Abstract
Description
Claims
Application Information

- Generate Ideas
- Intellectual Property
- Life Sciences
- Materials
- Tech Scout
- Unparalleled Data Quality
- Higher Quality Content
- 60% Fewer Hallucinations
Browse by: Latest US Patents, China's latest patents, Technical Efficacy Thesaurus, Application Domain, Technology Topic, Popular Technical Reports.
© 2025 PatSnap. All rights reserved.Legal|Privacy policy|Modern Slavery Act Transparency Statement|Sitemap|About US| Contact US: help@patsnap.com