Method of preparing and separating epichlorohydrin by chloropropene epoxidation
An epichlorohydrin and chloropropene technology, applied in chemical instruments and methods, organic chemistry, chemical recycling, etc., can solve the problems of complex regeneration, permanent deactivation, long process flow, etc., and achieve simplified process and process flow, Inhibition of side reaction products, reasonable effect of process route
- Summary
- Abstract
- Description
- Claims
- Application Information
AI Technical Summary
Problems solved by technology
Method used
Examples
Embodiment 1
[0027]Embodiment 1: 5 grams of allyl chloride (ALC) with a content of 98% in 500 grams, 170 grams of 50% hydrogen peroxide and 5 grams of promoter alkylphenol polyoxyethylene ether (OP) are dropped into a 1000 milliliter three-necked bottle, and 40 Gram catalyst phosphotungstic acid (three) hexadecylpyridine, and slowly warming up to 40 ℃ to stop heating, react under reflux state, after 60 minutes, the still temperature reaches 55 ℃, reflux stops, at this moment, the still liquid is cooled to 5 Below ℃, stand still, separate the liquid and solid, and the solid catalyst can continue to be used for the reaction. The liquid is layered in the separatory funnel, the upper layer is water, the lower layer is a mixture of epichlorohydrin and chloropropene (oil phase), the water is sampled and discarded, and the oil phase is collected and analyzed by gas chromatography. The composition of the oil phase is: ALC56. 2%, ECH42.2%, by-product 1.6%, the water phase contains ALC0.29%, ECH2.5%...
Embodiment 2
[0029] Embodiment 2: Allyl chloride, hydrogen peroxide, and catalyst promoter were added according to Embodiment 1, and the catalyst was recovered in Embodiment 1. The reaction was 90 minutes, and the selectivity of epichlorohydrin was 99.6%.
Embodiment 3
[0030] Embodiment 3: The formula is the same as that of Embodiment 1, the catalyst is recovered and reused from the vacuum distillation epichlorohydrin tower kettle, and the reaction is 100 minutes, and the epichlorohydrin selectivity is 98.8%.
PUM
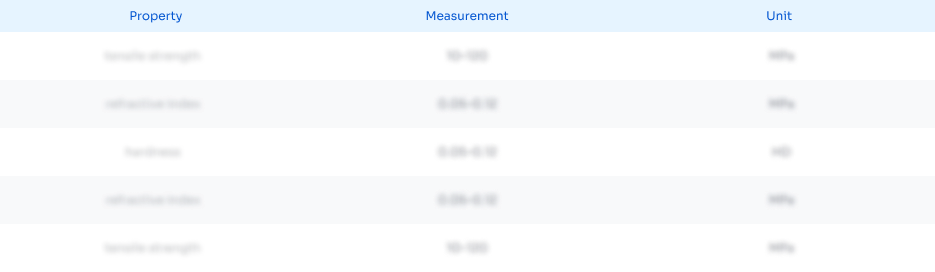
Abstract
Description
Claims
Application Information

- R&D Engineer
- R&D Manager
- IP Professional
- Industry Leading Data Capabilities
- Powerful AI technology
- Patent DNA Extraction
Browse by: Latest US Patents, China's latest patents, Technical Efficacy Thesaurus, Application Domain, Technology Topic, Popular Technical Reports.
© 2024 PatSnap. All rights reserved.Legal|Privacy policy|Modern Slavery Act Transparency Statement|Sitemap|About US| Contact US: help@patsnap.com