Device for reducing friction of guided region when forming high pressure in pipe
An internal high pressure forming and guiding area technology, applied in forming tools, metal processing equipment, manufacturing tools, etc., can solve the problems of reduced service life of molds, large friction in the guiding area, wear in the guiding area, etc., so as to improve the service life and reduce the tonnage. requirements, the effect of reducing the contact area
- Summary
- Abstract
- Description
- Claims
- Application Information
AI Technical Summary
Problems solved by technology
Method used
Image
Examples
specific Embodiment approach 1
[0007] Specific embodiment one: (referring to Fig. 1), present embodiment is made up of mold 8, left punch 7 and right punch 9, and described mold 8 is made up of upper mold 1 and lower mold 2 and upper mold 1 and lower mold 2 The molding cavity 10 is combined together. The left end of the mold 8 is provided with a left guide hole 16 communicating with the cavity 10, and the right end is provided with a right guiding hole 17 communicating with the cavity 10. The mold 8 is installed on a vertical press in a conventional manner. The axes of the punch 7 and the right punch 9 coincide with the axis of the mold 8, and the inside of the right punch 9 is provided with a liquid inlet 5 through which high-pressure liquid enters, and the left guide hole 16 and the right guide hole 17 of the mold 8 are counterbores. The center of the right end of the left punch 7 is provided with a right round table body 11 and the root of the right round table body 11 has a right guide ring groove 12, an...
specific Embodiment approach 2
[0009] Specific embodiment two: (referring to Fig. 2) the difference between this embodiment and specific embodiment one is: this embodiment also comprises the first polyurethane ring 13, and the inner shoulder end surface 18 of the left guide hole 16 and the left punch 7 A first polyurethane ring 13 is respectively housed between the peripheral circular ring end face 23 of the right guide hole 17 and the peripheral circular ring face 24 of the right punch 9 between the inner shoulder end face 19 of the right guide hole 17. When the punches on both sides move inward, the pipe end will expand under the action of the punch circular platform and fit to the inner wall of the outer ring of the punch to achieve a reliable seal; control the axial thrust and displacement of the punch and the pipe 3 The internal liquid pressure deforms the pipe material 3 and finally fits the wall of the mold cavity 10 to obtain a formed part. After the processing is completed, the part is taken out, an...
specific Embodiment approach 3
[0010] Specific embodiment three: (referring to Fig. 3) the difference between this embodiment and specific embodiment one is: this embodiment also comprises second polyurethane ring 14 and metal ring 15, and the inner shoulder end surface 18 of left guide hole 16 is connected with Two second polyurethane rings 14 are respectively housed between the peripheral annular end faces 23 of the left punch 7 and between the inner shoulder end faces 19 of the right guide hole 17 and the peripheral annular end faces 24 of the right punch 9, and each A metal ring 15 is arranged between the two second polyurethane rings 14 respectively. When the punches on both sides move inward, the pipe end will expand under the action of the punch circular platform and fit to the inner wall of the peripheral ring of the punch to achieve reliable sealing; control the axial thrust, displacement and pipe material of the punch 3 The internal liquid pressure deforms the pipe 3 and finally fits the wall of t...
PUM
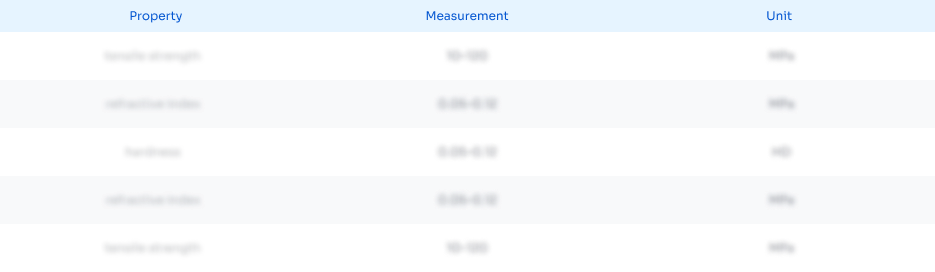
Abstract
Description
Claims
Application Information

- R&D
- Intellectual Property
- Life Sciences
- Materials
- Tech Scout
- Unparalleled Data Quality
- Higher Quality Content
- 60% Fewer Hallucinations
Browse by: Latest US Patents, China's latest patents, Technical Efficacy Thesaurus, Application Domain, Technology Topic, Popular Technical Reports.
© 2025 PatSnap. All rights reserved.Legal|Privacy policy|Modern Slavery Act Transparency Statement|Sitemap|About US| Contact US: help@patsnap.com