Forming die for optical element
A technology for forming molds and optical elements, which is applied in the direction of optical elements, household appliances, and other household appliances, etc., can solve the problems of reducing the molding thickness of optical elements, the quality of optical element molding products, and eccentricity, so as to avoid the modification of mold height Effect
- Summary
- Abstract
- Description
- Claims
- Application Information
AI Technical Summary
Problems solved by technology
Method used
Image
Examples
Embodiment Construction
[0011] The optical element forming mold provided by the present invention will be further described in detail below with reference to the accompanying drawings and embodiments.
[0012] Referring to FIG. 1 , the optical element forming mold 1 provided by the first embodiment of the present invention includes a first parting mold 10 and a second parting mold 20 matched with the first parting mold 10 .
[0013] Wherein, the second split mold 20 includes a second mold base 21 and a second mold core 22 embedded in the second mold base 21 . The second mold core 22 includes a matched first module 22a and a second module 22b. The first module 22a includes a mold cavity 221 and an insert 222 embedded in the mold cavity 221, and the insert 222 has a molding surface 222a. The second module 22b includes an opening 223 , and the central axis of the mold cavity 221 coincides with the central axis of the opening 223 . The second module 22b further includes a fixing block 224 and an adjust...
PUM
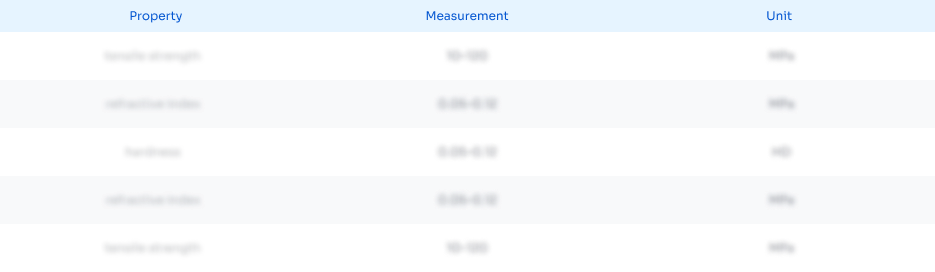
Abstract
Description
Claims
Application Information

- R&D Engineer
- R&D Manager
- IP Professional
- Industry Leading Data Capabilities
- Powerful AI technology
- Patent DNA Extraction
Browse by: Latest US Patents, China's latest patents, Technical Efficacy Thesaurus, Application Domain, Technology Topic, Popular Technical Reports.
© 2024 PatSnap. All rights reserved.Legal|Privacy policy|Modern Slavery Act Transparency Statement|Sitemap|About US| Contact US: help@patsnap.com