Method for preparing catalyst to purify automobile tail gas
A technology for purifying catalyst and automobile exhaust gas is applied to automobile exhaust gas purification catalyst and preparation thereof, three-way catalyst of HC and NOx and preparation thereof, and at the same time purifies the field of automobile exhaust gas CO, which can solve the problems of complex preparation process and achieve high activity, Overcome the effects of high temperature reduction and easy operation
- Summary
- Abstract
- Description
- Claims
- Application Information
AI Technical Summary
Problems solved by technology
Method used
Examples
Embodiment 1
[0023] To the mixed aqueous solution (the mass percent of each corresponding oxide is: Al 2 o 3 : 90wt%, CeO 2 : 5wt%, ZrO 2 : 2wt%, La 2 o 3 : 1wt%, Pr 6 o 11 : 1wt%, Y 2 o 3 : 1wt%), add 2vol% of Span 80, under stirring conditions, the above-mentioned mixed solution is added in the ammonium oxalate solution, the pH value is controlled to be 9.0, and the reaction time is 80 minutes to obtain the slurry containing the precipitate, Filter, wash with deionized water, bake at 200°C for 1 hour, and then bake at 800°C for 1 hour to obtain composite alumina. The composite alumina and deionized water are mixed at a weight ratio of 1:10, and ball milled on a ball mill to form a coating slurry. Dip the cordierite honeycomb carrier into the coating slurry, take it out after 60 seconds, blow off the slurry on the surface layer with compressed air, bake at 200°C for 1 hour, and bake at 800°C for 1 hour to obtain a coated composite oxide The carrier of the aluminum coating, the w...
Embodiment 2
[0025] To the mixed aqueous solution (the mass percent of each corresponding oxide is: Al 2 o 3 : 50wt%, CeO 2 : 25wt%, ZrO 2 : 5wt%, La 2 o 3 : 1wt%, Pr 6 o 11 : 15wt%, Y 2 o 3 : 2wt%, Fe 2 o 3 : 1wt%, MnO 2 : 1wt%), add 1vol% sodium dodecyl sulfonate, under stirring condition, above-mentioned mixed solution is joined in the ammonium carbonate solution, and pH value is controlled as 4.5, and the reaction time is 40 minutes, obtains containing precipitate The slurry was filtered, washed with deionized water, cooled and dried at room temperature for 24 hours, and then calcined at 400°C for 6 hours to obtain composite alumina. The composite alumina and deionized water are mixed at a weight ratio of 1:5, and ball milled on a ball mill to form a coating slurry. Immerse the cordierite honeycomb carrier into the coating slurry, take it out after 10 seconds, blow off the slurry on the surface layer with compressed air, let it cool and dry at room temperature for 24 hours,...
Embodiment 3
[0027] To the mixed aqueous solution (the mass percent of each corresponding oxide is: Al 2 o 3 : 50wt%, CeO 2 : 15wt%, ZrO 2 : 15wt%, La 2 o 3 : 7wt%, Pr 6 o 11 : 2wt%, Y 2 o 3 : 3wt%, CuO: 5wt%, BaO: 3wt%), add 2vol% of Span 80, under stirring condition, ammonium oxalate solution is added in the above mixed solution, the pH value is controlled to be 9.0, and the reaction time is 80 Minutes to obtain a slurry containing precipitates, filter, wash with deionized water, bake at 80°C for 6 hours, and then bake at 500°C for 6 hours to obtain composite alumina. The composite alumina and deionized water are mixed at a weight ratio of 1:10, and ball milled on a ball mill to form a coating slurry. Dip the cordierite honeycomb carrier into the coating slurry, take it out after 30 seconds, blow off the slurry on the surface layer with compressed air, bake at 80°C for 6 hours, and then bake at 500°C for 6 hours to obtain a coated The carrier of the composite alumina coating, t...
PUM
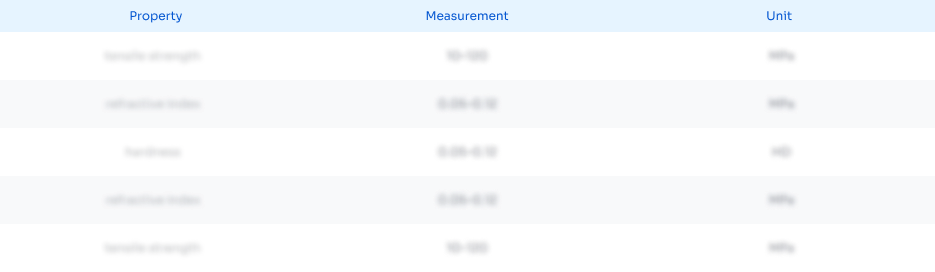
Abstract
Description
Claims
Application Information

- Generate Ideas
- Intellectual Property
- Life Sciences
- Materials
- Tech Scout
- Unparalleled Data Quality
- Higher Quality Content
- 60% Fewer Hallucinations
Browse by: Latest US Patents, China's latest patents, Technical Efficacy Thesaurus, Application Domain, Technology Topic, Popular Technical Reports.
© 2025 PatSnap. All rights reserved.Legal|Privacy policy|Modern Slavery Act Transparency Statement|Sitemap|About US| Contact US: help@patsnap.com