Cast iron series mould material thermal treatment method capable of acquiring controllable and uniform rigidity
A heat treatment method and mold material technology, applied in the field of heat treatment, can solve the problem of not mentioning the heat treatment method of cast iron mold materials, etc., and achieve the effect of good hardenability
- Summary
- Abstract
- Description
- Claims
- Application Information
AI Technical Summary
Problems solved by technology
Method used
Image
Examples
Embodiment 1
[0026] Obtain heat treatment for cast iron mold target hardness 33HRC, material is HT300
[0027] (1) Normalizing pretreatment: the material HT300 is placed in a vacuum annealing furnace, and the vacuum degree is pumped to 1×10 -1 Pa, then preheat to 900°C, hold for 180 minutes to austenitize, leave the vacuum furnace and air cool to obtain a uniform balanced structure;
[0028] (2) Oil cooling and quenching: Put the workpiece processed in step (1) into the vacuum oil quenching furnace, and the vacuum degree is 1×10 -1 Pa, then raise the temperature to 600°C at a heating rate of 10°C / min, hold for 50 minutes, then raise the temperature to 890°C at a heating rate of 5°C / min, leave the vacuum furnace after holding for 100 minutes, and quench with oil cooling to obtain horse body tissue;
[0029] (3) Put the workpiece processed in step (2) into the vacuum tempering furnace, and the vacuum degree is 1×10 -1 Pa, and then tempered three times with variable temperature:
[0030] ...
Embodiment 2
[0035] Obtain heat treatment for cast iron mold target hardness 45HRC, material is QT600
[0036] (1) Normalizing pretreatment: material QT600 is placed in a vacuum annealing furnace, and the vacuum degree is pumped to 1×10 -1 Pa, then preheat to 920°C, hold for 180 minutes to austenitize, and air-cool after leaving the vacuum furnace to obtain a uniform balanced structure;
[0037] (2) Oil cooling and quenching: Put the workpiece processed in step (1) into the vacuum oil quenching furnace, and the vacuum degree is 1×10 -1 Pa, then raise the temperature to 620°C at a heating rate of 10°C / min, hold for 50 minutes, then raise the temperature to 890°C at a heating rate of 5°C / min, leave the furnace after holding for 100 minutes, and quench by oil cooling to obtain martensite organize;
[0038] (3) Put the workpiece processed in step (2) into the vacuum tempering furnace, and the vacuum degree is 1×10 -1 Pa, and then tempered three times with variable temperature:
[0039] Tem...
Embodiment 3
[0044] Heat treatment to obtain cast iron mold target hardness 55HRC, material is MoCr cast iron
[0045] (1) Normalizing pretreatment: the material MoCr cast iron is placed in a vacuum annealing furnace, and the vacuum degree is pumped to 1×10 -1 Pa, then preheat to 950°C, hold for 180 minutes to austenitize, and air-cool after leaving the vacuum furnace to obtain a uniform balanced structure;
[0046] (2) Oil cooling and quenching: Put the workpiece processed in step (1) into the vacuum oil quenching furnace, and the vacuum degree is 1×10 -1 Pa, then raise the temperature to 650°C at a heating rate of 10°C / min, keep it warm for 50 minutes, then raise the temperature to 900°C at a heating rate of 5°C / min, keep it for 100 minutes, take it out of the furnace, and quench it with oil cooling to obtain martensite organize;
[0047] (3) Put the workpiece processed in step (2) into the vacuum tempering furnace, and the vacuum degree is 1×10 -1 Pa, and then the vacuum furnace is t...
PUM
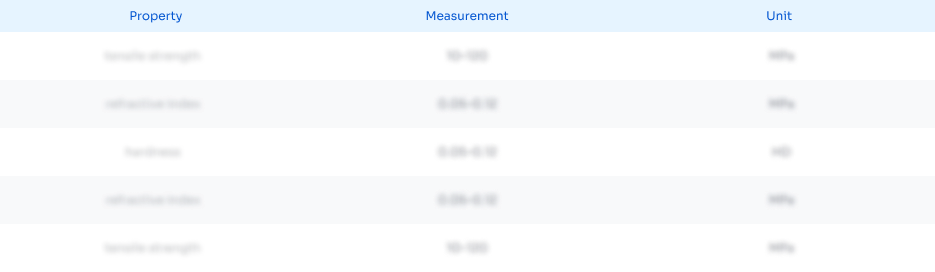
Abstract
Description
Claims
Application Information

- R&D Engineer
- R&D Manager
- IP Professional
- Industry Leading Data Capabilities
- Powerful AI technology
- Patent DNA Extraction
Browse by: Latest US Patents, China's latest patents, Technical Efficacy Thesaurus, Application Domain, Technology Topic, Popular Technical Reports.
© 2024 PatSnap. All rights reserved.Legal|Privacy policy|Modern Slavery Act Transparency Statement|Sitemap|About US| Contact US: help@patsnap.com