Process for preparing expanded product of thermoplastic resin
A technology of thermoplastic resin and foamed products, which is applied in the field of preparing thermoplastic resin foamed products, can solve the problems of appearance, mechanical properties, barrier performance, poor foaming ratio, uneven size distribution, low number of cells, etc., to achieve good Physical and mechanical properties, effective cell diameter, and the effect of increasing nucleation density
- Summary
- Abstract
- Description
- Claims
- Application Information
AI Technical Summary
Problems solved by technology
Method used
Image
Examples
Embodiment 1
[0029] The preparation of embodiment 1, PMMA foamed product
[0030] The vacuum-dried polymethyl methacrylate (PMMA) was melted and pressed at 200° C., and quenched in cold water to prepare a 1 mm thick sample.
[0031] The above PMMA sample was placed in an autoclave, and 20°C / 12MPa CO 2 After 6 hours of constant temperature and pressure, the sample was taken out from the autoclave, and foamed in a water bath and a water bath with ultrasonic waves applied (ultrasonic power is 100W, ultrasonic frequency is 20kHz), the foaming temperature is 80°C, and the foaming time is 20s.
[0032] Figure 1A Electron micrograph of the section of PMMA products without ultrasonic waves, Figure 1B It is an electron micrograph of the section of PMMA products with ultrasonic waves applied. The results show that after ultrasonic waves are applied, the foaming ratio of the foamed PMMA increases from 2.3 to 4.6 without ultrasonic waves, and the cell diameter decreases from 14.0 μm to 4.2 μm. De...
Embodiment 2
[0033] Embodiment 2, the preparation of PS foamed product
[0034] The vacuum-dried polystyrene (PS) was heated to 200° C., kept for 3 minutes, and quenched in cold water to prepare a 1 mm thick sample.
[0035] The above PS sample was placed in an autoclave, and 40°C / 8MPa CO 2 After 6 hours of constant temperature and pressure, the sample was taken out of the autoclave, and foamed in a water bath and a water bath with ultrasonic waves (ultrasonic power 200W, ultrasonic frequency 20kHz), the foaming temperature was 80°C, and the foaming time was 20s.
[0036] Figure 2A It is the electron micrograph of the section of the PS product without ultrasonic waves, Figure 2B It is an electron micrograph of the cross-section of PS products with ultrasonic waves applied. The results show that after ultrasonic waves are applied, the foaming ratio of foamed PS increases from 1.3 to 2.4 without ultrasonic waves, and the cell density increases from 7.5×10 10 cells / cm 3 Increased to 2.3...
Embodiment 3
[0037] Embodiment 3, the preparation of PC foam product
[0038] The vacuum-dried polycarbonate (PC) was melted and pressed at 260° C., and quenched in cold water to prepare a 1 mm thick sample.
[0039] Put the above PC sample into an autoclave, and pass through CO at 20°C / 20MPa 2 After 10 hours of constant temperature and pressure, the sample was taken out from the autoclave, and foamed in a glycerin bath and a glycerin bath with ultrasonic waves (ultrasonic power 100W, ultrasonic frequency 20kHz), the foaming temperature was 100 ° C, and the foaming time was 30s.
[0040] Figure 3A It is an electron micrograph of the PC product section without ultrasonic waves, Figure 3B It is an electron microscope photo of the PC product section with ultrasonic waves applied. The results show that after ultrasonic waves are applied, the foaming ratio of the foamed PC increases from 1.1 to 1.7 without ultrasonic waves, the cell diameter decreases from 2.4 μm to 2.1 μm, and the cell de...
PUM
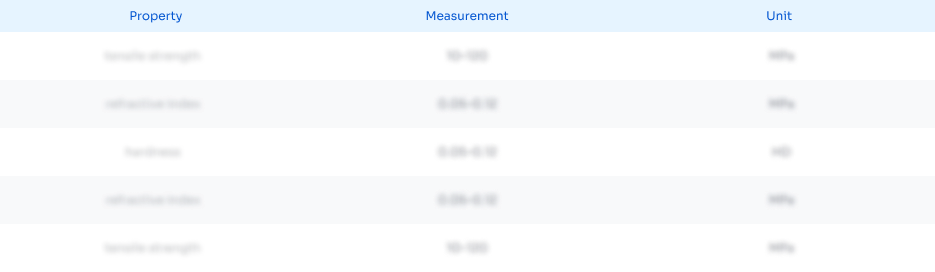
Abstract
Description
Claims
Application Information

- R&D
- Intellectual Property
- Life Sciences
- Materials
- Tech Scout
- Unparalleled Data Quality
- Higher Quality Content
- 60% Fewer Hallucinations
Browse by: Latest US Patents, China's latest patents, Technical Efficacy Thesaurus, Application Domain, Technology Topic, Popular Technical Reports.
© 2025 PatSnap. All rights reserved.Legal|Privacy policy|Modern Slavery Act Transparency Statement|Sitemap|About US| Contact US: help@patsnap.com