Sintering method for high-chromic vanadium-titanium ferroferrite
A technology of vanadium-titanium magnetite and sintering method, which is applied in the field of iron and steel metallurgy to achieve the effects of improving mineral composition and structure, improving gas permeability, and improving quality and output
- Summary
- Abstract
- Description
- Claims
- Application Information
AI Technical Summary
Problems solved by technology
Method used
Examples
Embodiment 1
[0018] Sintered red grid high chromium vanadium-titanium magnetite concentrate, sintering basicity is 2.2, the content of quicklime involved in the pre-granulation of the mixture is 3%, and the pre-wetting moisture of the returned ore is 8%, B 2 O 3 The addition amount is 0.5%, and the MgO content in the sinter is 2.8%.
[0019] The results show that compared with the reference period, the melting point of the sinter mixture is reduced by 51°C, the calcium ferrite content in the sinter is increased by 5 percentage points, the drum strength of the sinter is increased by 1.09 percentage points, the yield rate is increased by 1.27 percentage points, and the output is increased by 4.2%. The low-temperature reduction and pulverization rate of sinter decreased by 4.03 percentage points.
Embodiment 2
[0021] Sintered red grid high chromium vanadium-titanium magnetite concentrate, sintering basicity is 2.3, the content of quicklime involved in the pre-granulation of the mixture is 4%, and the pre-wetting moisture of the returned ore is 9.5%, B 2 O 3 The addition amount is 0.7%, and the MgO content in the sinter is 3.2%.
[0022] The results show that compared with the base period, the melting point of the sinter mixture is reduced by 58℃, the calcium ferrite content in the sinter is increased by 8%, the drum strength of the sinter is increased by 1.31%, the yield rate is increased by 2.46%, and the output is increased by 4.63%. The low-temperature reduction pulverization rate of sinter decreased by 4.52%.
Embodiment 3
[0024] Sintered red grid high chromium vanadium-titanium magnetite concentrate, sintering basicity is 2.35, the content of quicklime participating in the pre-granulation of the mixture is 4.5%, and the pre-wetting moisture of the returned ore is 10%, B 2 O 3 The addition amount is 0.8%, and the MgO content in the sinter is 3.5%.
[0025] The results show that compared with the reference period, the melting point of the sinter mixture is reduced by 62℃, the calcium ferrite content in the sinter is increased by 12%, the drum strength of the sinter is increased by 1.45%, the yield is increased by 3.0%, and the output is increased by 4.81%. The low-temperature reduction pulverization rate of sinter decreased by 5.4%.
PUM
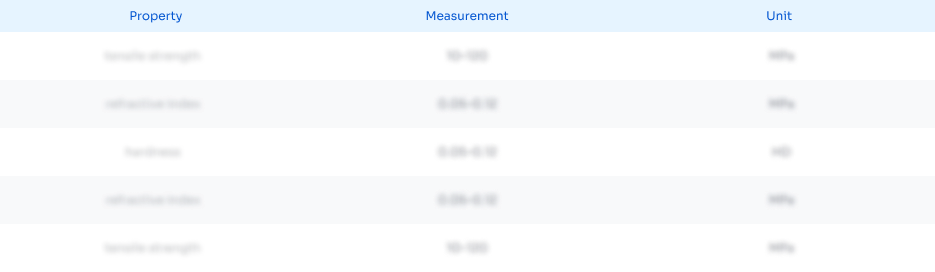
Abstract
Description
Claims
Application Information

- R&D
- Intellectual Property
- Life Sciences
- Materials
- Tech Scout
- Unparalleled Data Quality
- Higher Quality Content
- 60% Fewer Hallucinations
Browse by: Latest US Patents, China's latest patents, Technical Efficacy Thesaurus, Application Domain, Technology Topic, Popular Technical Reports.
© 2025 PatSnap. All rights reserved.Legal|Privacy policy|Modern Slavery Act Transparency Statement|Sitemap|About US| Contact US: help@patsnap.com