Iron concentrate powder dustproof agent and preparation method thereof
A technology of iron concentrate powder and anti-dust agent, which is applied in the direction of chemical instruments and methods, and other chemical processes, and can solve the problems of polluted site operation environment, dust injury of operators, and flying dust formed by iron ore powder, so as to improve operation environment, reduce dust hazards, and prevent flying effect
- Summary
- Abstract
- Description
- Claims
- Application Information
AI Technical Summary
Problems solved by technology
Method used
Examples
Embodiment 1
[0032] 1. Measure 620Kg of water and put it into a 1000L enamel reaction kettle, put 2Kg of water-soluble polyacrylamide into the reaction kettle under stirring, and then put in 50Kg of polyvinyl alcohol resin. When it reaches 90°C, stop heating, maintain the temperature in the reactor at 90°C, and dissolve for 40 minutes;
[0033] 2. After dissolving, cool down to 66°C, put 5Kg of dibutyl phthalate into the reactor, then add 120Kg of magnesium chloride and 50Kg of calcium chloride, and dissolve for 30 minutes;
[0034] 3. Cool down to 60°C and add a solution made of 40Kg calcium lignosulfonate and 107Kg water, then add 5Kg each of ethylene glycol and diethylene glycol;
[0035] 4. Continue to stir for 30 minutes to make it a uniform solution;
[0036] 5. Cool down to 40°C and filter through a sieve to become the finished product.
Embodiment 2
[0038] 1. Measure 620Kg of water and put it into a 1000L enamel reaction kettle. Put 2Kg of water-soluble polyacrylamide into the reaction kettle under stirring, and then put in 72Kg of water-soluble acrylic resin. When it reaches 90°C, stop heating, maintain the temperature in the reactor at 90°C, and dissolve for 40 minutes;
[0039] 2. After dissolving, cool down to 66°C, put 10Kg of dibutyl phthalate into the reactor, then add 120Kg of magnesium chloride and 50Kg of calcium chloride, and dissolve for 30 minutes;
[0040] 3. Cool down to 60°C and add a solution made of 60Kg sodium lignosulfonate and 107Kg water, then add 15Kg each of ethylene glycol and diethylene glycol;
[0041] 4. Continue to stir for 30 minutes to make it a uniform solution;
[0042] 5. Cool down to 40°C and filter through a sieve to become the finished product.
Embodiment 3
[0044] 1. Measure 570Kg of water and put it into a 1000L enamel reaction kettle, put 2Kg of water-soluble polyacrylamide into the reaction kettle under stirring, and heat up the steam after the injection is completed. When the temperature reaches 90°C, stop heating and maintain the reaction kettle The internal temperature is 90°C, dissolve for 30 minutes, and then add 100Kg of water-soluble alkyd resin with a concentration of 50%, and dissolve for 30 minutes;
[0045] 2. After dissolving, lower the temperature to 66°C, put 20Kg of dioctyl phthalate into the reactor, then add 350Kg of magnesium chloride and 150Kg of calcium chloride, and dissolve for 30 minutes;
[0046] 3. Cool down to 60°C and add a solution made of 40Kg sodium carboxymethylcellulose and 107Kg water, then add 5Kg each of ethylene glycol and diethylene glycol;
[0047] 4. Continue to stir for 30 minutes, add 1Kg each of cobalt naphthenate and manganese naphthenate to make a uniform solution; 5. Cool down to 40...
PUM
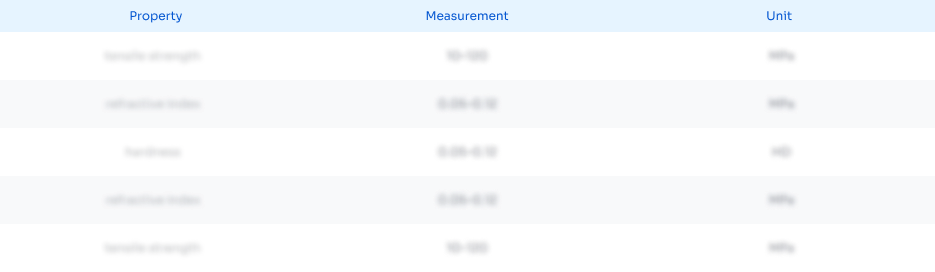
Abstract
Description
Claims
Application Information

- R&D Engineer
- R&D Manager
- IP Professional
- Industry Leading Data Capabilities
- Powerful AI technology
- Patent DNA Extraction
Browse by: Latest US Patents, China's latest patents, Technical Efficacy Thesaurus, Application Domain, Technology Topic, Popular Technical Reports.
© 2024 PatSnap. All rights reserved.Legal|Privacy policy|Modern Slavery Act Transparency Statement|Sitemap|About US| Contact US: help@patsnap.com