Manipulator device
A technology of manipulator and first arm, applied in the direction of manipulator, program-controlled manipulator, mechanical equipment, etc., can solve the problems such as the inability to transmit parts 952 to reach, affecting the running accuracy, deformation, etc.
- Summary
- Abstract
- Description
- Claims
- Application Information
AI Technical Summary
Problems solved by technology
Method used
Image
Examples
Embodiment Construction
[0053] In the following detailed description, the same symbols and reference numerals correspond to the same components in each drawing.
[0054] 1 to 4 show a first preferred embodiment of the manipulator device 100 of the present invention. The first embodiment of the manipulator device 100 shown in Figure 1 comprises a first arm linkage mechanism 110, a second arm linkage mechanism 120, a linkage holding mechanism 140, a manipulator drive mechanism 130, a manipulator component 151 , and a transmission component 152 .
[0055] The first arm linkage mechanism 110 consists of a four-bar crank chain, which includes a first arm link 111, a second arm link 112, a third arm link 113, and a first arm link 113. Four arm links 114 , wherein the second arm link 112 is substantially parallel to the first arm link 111 , and the fourth arm link 114 is basically parallel to the third arm link 113 . The second arm linkage mechanism 120 is composed of a second four-bar crank chain, which ...
PUM
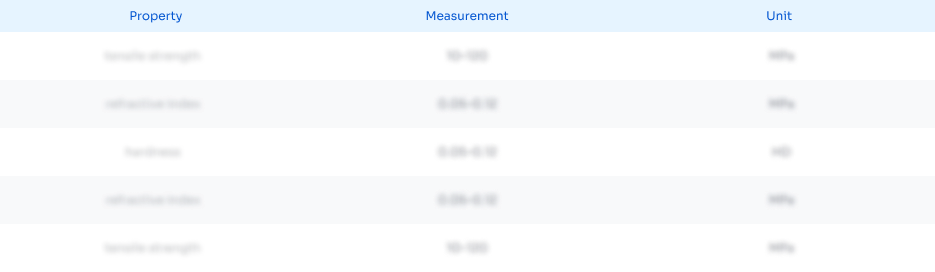
Abstract
Description
Claims
Application Information

- R&D
- Intellectual Property
- Life Sciences
- Materials
- Tech Scout
- Unparalleled Data Quality
- Higher Quality Content
- 60% Fewer Hallucinations
Browse by: Latest US Patents, China's latest patents, Technical Efficacy Thesaurus, Application Domain, Technology Topic, Popular Technical Reports.
© 2025 PatSnap. All rights reserved.Legal|Privacy policy|Modern Slavery Act Transparency Statement|Sitemap|About US| Contact US: help@patsnap.com