Method and structure of preventing channel of reactor for preparing ethyne by cracking plasma coal from coking
A plasma and coal cracking technology, applied in the field of ionized coal cracking to produce acetylene, to avoid scour loss, prevent coking, and increase conversion rate
- Summary
- Abstract
- Description
- Claims
- Application Information
AI Technical Summary
Problems solved by technology
Method used
Image
Examples
example 1
[0022] The structure to prevent the coking of the plasma coal cracking acetylene reactor, including the plasma reactor 1, the plasma jet 2 generated by the plasma reactor 1 enters the jet channel 3, and the lower part of the jet channel 3 is divided into coal powder and plasma jet 2 The mixing section 4 has a pulverized coal pipeline 5 leading into the mixing section 4, and around the passage at the bottom of the mixing section 4, there is a combustion chamber 6 surrounding the passage, and an air inlet 7 is arranged on the combustion chamber 6. On the annular inner wall of the combustion chamber 6 There is an annular slit 12 between the passage inner wall 10 and the combustion chamber 6 below.
[0023] The pulverized coal transported into the plasma jet 2 and the pulverized coal pipeline 5 is quickly mixed in the mixing section 4, the pulverized coal is quickly heated and gasified, and acetylene is generated in the plasma reaction section 9, and the rapidly combustible hydroge...
example 2
[0026]The output power of the plasma torch is 2MW, the pulverized coal delivery rate is 1200kg / h, and the inner wall diameter of the reactor is Φ100mm. Using natural gas and pure oxygen to generate high-temperature and high-pressure gas, the high-temperature and high-pressure gas is ejected from the Φ95mm×2mm annular slit to form a high-temperature and high-speed gas film, and the annular slit is 40mm away from the pulverized coal pipeline. Adjust the ratio of natural gas and oxygen during normal operation, and the combustion flame atmosphere is weak reducing atmosphere. After a long time of operation, the internal pressure of the reactor will rise, and the coking on the inner wall of the reactor will reduce the area of the reaction channel, which is caused by the pressure drop in the reaction section. The internal pressure of the device rises gradually, but after the rising pressure is greater than 0.01Mpa of the normal operating pressure, the ratio of natural gas and oxygen...
PUM
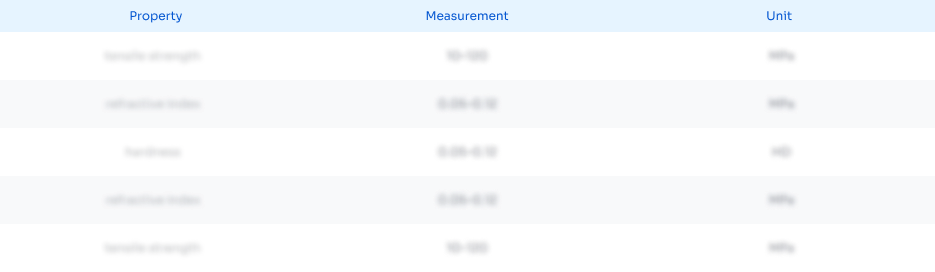
Abstract
Description
Claims
Application Information

- R&D
- Intellectual Property
- Life Sciences
- Materials
- Tech Scout
- Unparalleled Data Quality
- Higher Quality Content
- 60% Fewer Hallucinations
Browse by: Latest US Patents, China's latest patents, Technical Efficacy Thesaurus, Application Domain, Technology Topic, Popular Technical Reports.
© 2025 PatSnap. All rights reserved.Legal|Privacy policy|Modern Slavery Act Transparency Statement|Sitemap|About US| Contact US: help@patsnap.com