Process for preparation of self-spread high-temperature synthesizing low cost ª‡-sialon powder
A self-propagating high-temperature, low-cost technology, applied in the field of high-temperature self-propagating process synthesis powder, low-cost synthesis of α-sialon powder, can solve the problem of high cost of silicon nitride and aluminum nitride, to slow down the reaction speed, The effect of reducing the impurity content of the system and reducing the production cost
- Summary
- Abstract
- Description
- Claims
- Application Information
AI Technical Summary
Problems solved by technology
Method used
Image
Examples
Embodiment 1
[0029] Taking blast furnace slag, metallic silicon powder, and aluminum powder from a certain iron and steel plant as raw materials, and 5% Sialon powder synthesized by the technology of the present invention, considering the chemical composition of slag (Table 1), the composition of α-Sialon is calculated by Ca 0.71 Mg 0.23 Si 9.18 Al 2.82 o 0.94 N 15.06 According to the design, the raw materials prepared according to this component are mixed in a nylon barrel with silicon nitride balls as the medium, and after 48 hours of dry-mixed ball milling, they are loosely packed in an upright ring-shaped cylinder made of carbon felt with an outer diameter of φ60mm×inner diameter of φ55mm×a height of φ60mm ( figure 2 As shown), put it into a self-propagating high-temperature synthesis furnace, and fill it with 15Mpa high-pressure nitrogen (purity 99.99%) after vacuuming. The synthesis atmosphere is high-pressure nitrogen, self-propagating combustion after ignition, and Sialon powd...
Embodiment 2
[0033] Adopt the same process of embodiment 1, just change to limestone powder (CaCO 3 >98wt%) instead of blast furnace slag, it is made raw material with metal silicon powder, aluminum powder and 15% Sialon powder synthesized by the present invention, and the composition of Ca-α-Sialon is Ca 0.8 Si 8.8 al 3.2 o 1.6 N 14.4 Design, synthesize Ca-α-Sialon by high-temperature self-propagating process, and the synthesized powder is determined as single-phase Ca-α-Sialon by XRD.
Embodiment 3
[0035] Adopt the same process of embodiment 1, just replace blast furnace slag with Bai Yunshi powder instead, it makes raw material with metal silicon powder, aluminum powder and 30% Sialon powder synthesized by the present invention, and the composition design of Ca-α-Sialon is in the whole Ca (Ca, Mg)-α-Sialon can be synthesized by high-temperature self-propagating process through the change in the -α-Sialon phase region. Specifically, press M x Si 12-3x al 3x al 3x o 2x N 16-2x Component design, any point in 0.4<x<1.4 can be selected. β-Sialon is designed according to the amount of silicon and aluminum. The rest of the conditions are the same as in Example 1, and (Ca, Mg)-α-Sialon powder is obtained.
PUM
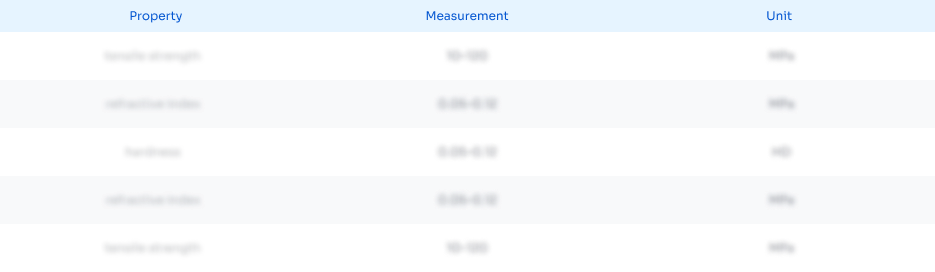
Abstract
Description
Claims
Application Information

- R&D
- Intellectual Property
- Life Sciences
- Materials
- Tech Scout
- Unparalleled Data Quality
- Higher Quality Content
- 60% Fewer Hallucinations
Browse by: Latest US Patents, China's latest patents, Technical Efficacy Thesaurus, Application Domain, Technology Topic, Popular Technical Reports.
© 2025 PatSnap. All rights reserved.Legal|Privacy policy|Modern Slavery Act Transparency Statement|Sitemap|About US| Contact US: help@patsnap.com