Method for producing a coupling on a pipe and device for producing said coupling
一种喇叭口、管子的技术,应用在在管子上加工喇叭口和用于形成喇叭口的装置领域,能够解决泄漏等问题,达到节省材料费用、壁厚增加的效果
- Summary
- Abstract
- Description
- Claims
- Application Information
AI Technical Summary
Problems solved by technology
Method used
Image
Examples
Embodiment Construction
[0016] figure 1 The processed pipe 1 shown in has a wall thickness d1 corresponding to the original pipe wall thickness. After two-step flaring, the tube has a first conical portion 5, an adjoining first cylindrical portion 7 having a wall thickness d7 that decreases in relation to the wall thickness d1 according to the degree of flaring, a second conical portion 6, adjoining The second cylindrical part 8 and the inwardly curved flange 9. The second cylindrical part 8 has a wall thickness d8 which is increased to the required extent by the upsetting step according to the invention before the flange 9 is provided. Wall thickness d8 should be at least equal to wall thickness d7. It has even been found to be advantageous to increase said wall thickness to wall thickness d1.
[0017] exist figure 2 , the multi-step flaring tool 2 has been pressed into the pipe end in the axial direction. The shape of the flare with sections 5 to 8 is formed internally by sections 5' to 8' of...
PUM
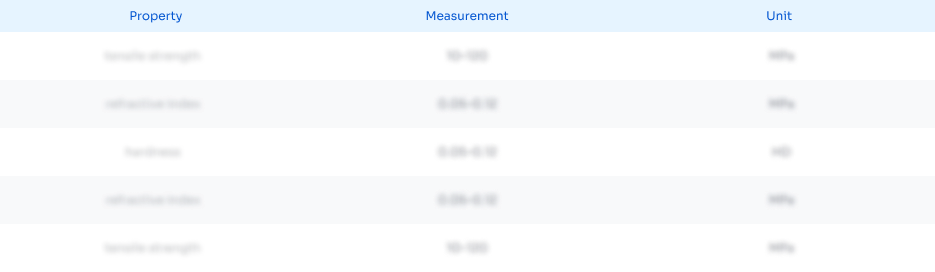
Abstract
Description
Claims
Application Information

- R&D
- Intellectual Property
- Life Sciences
- Materials
- Tech Scout
- Unparalleled Data Quality
- Higher Quality Content
- 60% Fewer Hallucinations
Browse by: Latest US Patents, China's latest patents, Technical Efficacy Thesaurus, Application Domain, Technology Topic, Popular Technical Reports.
© 2025 PatSnap. All rights reserved.Legal|Privacy policy|Modern Slavery Act Transparency Statement|Sitemap|About US| Contact US: help@patsnap.com