Combined mould for precasting ring-type forge piece cast steel billet
A combined mold and ring forging technology, which is applied in the field of mechanical forging and casting, can solve the problems of mold bodies stuck together and cannot be separated, cracks or cracks, scrapping, etc., to reduce production costs, simplify forging process, and simple method and structure Effect
- Summary
- Abstract
- Description
- Claims
- Application Information
AI Technical Summary
Problems solved by technology
Method used
Image
Examples
Embodiment Construction
[0013] The present invention will be further described below in conjunction with accompanying drawing:
[0014] In Fig. 1 and Fig. 2: annular casting billet 1, lower mold body 2, inner ring body 3, small ring block 4, small wedge block 5, annular surface 6.
[0015] In the embodiment shown in the drawings, the inner ring body 3 of combined structure is provided in the annular cavity of the lower mold body 2, and the inner ring body 3 is arranged in the concave step at the bottom of the cavity of the lower mold body 2, and the inner ring body 3 The ring body 3 is composed of two small ring blocks 4 and two small wedge blocks 5 respectively. The upper end surface, and the annular outer surface of the inner ring body 3, that is, the cavity surface in contact with the annular cast billet 1, is provided with a concave isosceles triangular annular surface 6, and the draft slope is not selected.
[0016] During use, it is enough to assemble the inner ring body 3 of the combined stru...
PUM
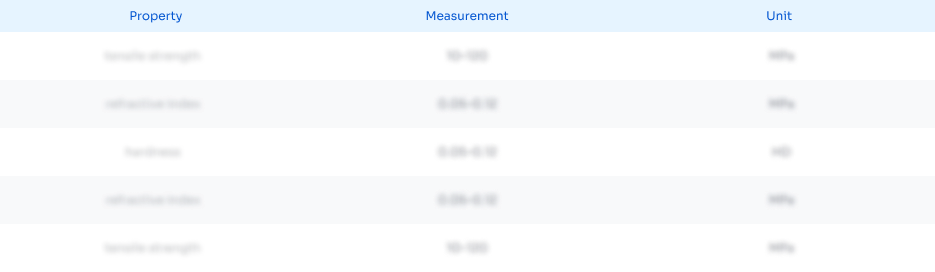
Abstract
Description
Claims
Application Information

- Generate Ideas
- Intellectual Property
- Life Sciences
- Materials
- Tech Scout
- Unparalleled Data Quality
- Higher Quality Content
- 60% Fewer Hallucinations
Browse by: Latest US Patents, China's latest patents, Technical Efficacy Thesaurus, Application Domain, Technology Topic, Popular Technical Reports.
© 2025 PatSnap. All rights reserved.Legal|Privacy policy|Modern Slavery Act Transparency Statement|Sitemap|About US| Contact US: help@patsnap.com