Forging molding technological method for multi-lug part
A technology of forging molding and process method, applied in the field of forging, can solve the problems of large flash rate of blanks, noise pollution, waste of time, manpower, etc., and achieve the effects of simple forging process, improvement of production efficiency, and reduction of waste of blanks
- Summary
- Abstract
- Description
- Claims
- Application Information
AI Technical Summary
Problems solved by technology
Method used
Image
Examples
Embodiment
[0019] A kind of forging forming process method of multiple lug parts, taking the crankshaft as an example to complete according to the following steps:
[0020] a. Heating for blanking: heating the round bar blank after blanking.
[0021] b. Flattening: if figure 1 As shown in the four figures on the left side of the middle, one end of the round bar blank is placed on the pressing die 1, and one end of the round bar blank is flattened after the pressing die 1 is closed once.
[0022] c. Pier rough pressing: such as figure 1 As shown in the four figures on the right side of the middle, the flattened end of the round bar blank is vertically inserted into the "V"-shaped groove 3a of the blank-making cavity of the pressing die 1, and the other end of the round bar blank is roughly pressed, thereby A blank whose contour matches the cavity of the pre-forging die is obtained; the two-step process of steps b and c is completed on one pressing die 1 .
[0023] d. Forging molding:...
PUM
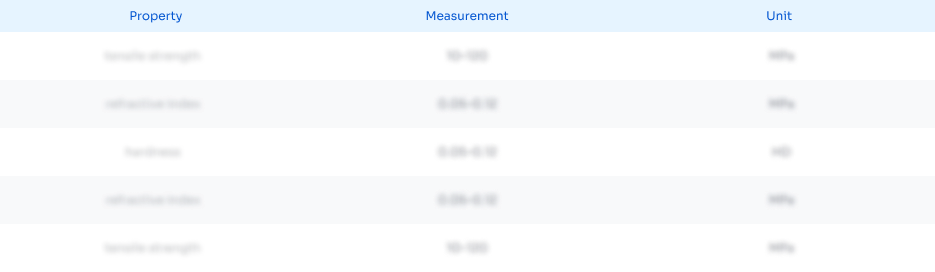
Abstract
Description
Claims
Application Information

- R&D Engineer
- R&D Manager
- IP Professional
- Industry Leading Data Capabilities
- Powerful AI technology
- Patent DNA Extraction
Browse by: Latest US Patents, China's latest patents, Technical Efficacy Thesaurus, Application Domain, Technology Topic, Popular Technical Reports.
© 2024 PatSnap. All rights reserved.Legal|Privacy policy|Modern Slavery Act Transparency Statement|Sitemap|About US| Contact US: help@patsnap.com