Method for preparing nano fiber endless tow
A nanofiber, filament bundle technology, applied in fiber processing, filament/thread forming, textile and papermaking, etc., can solve the problems of loss, fiber scattering, low efficiency, etc., to avoid scattering and loss, improve production efficiency, Simple to use effects
- Summary
- Abstract
- Description
- Claims
- Application Information
AI Technical Summary
Problems solved by technology
Method used
Image
Examples
preparation example Construction
[0021] A method for preparing nano-fiber filament bundles adopts a spinning box body, two rows of electrospinning nozzles with opposite nozzles are placed in parallel at the same height at the top of the spinning box body, and several groups of godet rollers are arranged in the middle of the spinning box body Yes, the distance between the godet roller pair and the electrospinning nozzles of the two rows of nozzles is equal. The specific preparation steps of a nanofiber filament bundle are as follows: (1) The high polymer solution is delivered to the electrospinning nozzle in the spinning box of the nanofiber filament bundle; (2) The electrospinning nozzles of the two rows of nozzles are opposite. Apply DC high voltages of opposite polarity 10KV-100KV: (3) The polymer solution at the top of the electrospinning nozzle stretches and whips to form charged nanofibers under the action of the electric field force, and the electrospinning nozzles with opposite nozzles spray The produced n...
Embodiment 1
[0024] 100g of polyacrylonitrile PAN is dissolved in 1000ml of N,N-dimethylformamide, and the high polymer solution is delivered to two rows of 100 electrospinning nozzles in each of the nanofiber filament bundle spinning boxes. The distance between the rows of electrospinning nozzles in the spinning box is 5 cm, and the distance between the electrospinning nozzles of the two rows of nozzles is 10 cm. The electrospinning nozzles of the two rows of nozzles facing each other are respectively applied with a DC high voltage of ±20kv of opposite polarity, and the inner diameter of the electrospinning nozzle is 0.5mm. The godet roller draws the filament bundle at a speed of 3cm / s. The nanofibers ejected from the top of the electro-spinning nozzle are drawn by the godet roller to form filament bundles and are exported and collected.
Embodiment 2
[0026] 100g of poly-L-lactic acid PLLA (viscosity average molecular weight 100,000) is dissolved in a mixed solvent of 500ml acetone and 500ml N, N-dimethylformamide, and the polymer solution is delivered to the spinning box of nanofiber filament bundles There are 100 electrospinning nozzles in each of the two rows. The distance between the nozzles in each row of electrospinning nozzles is 30cm, and the distance between the electrospinning nozzles of the two rows of nozzles is 50cm. The electrospinning nozzles of the two rows of nozzles opposite to each other are respectively applied with a DC high voltage of ±10kv of opposite polarity, and the inner diameter of the electrospinning nozzle is 0.2mm. The godet roller draws the filament bundle at a speed of 6cm / s. The nanofibers ejected from the top of the electro-spinning nozzle are drawn by the godet roller to form filament bundles and are exported and collected.
PUM
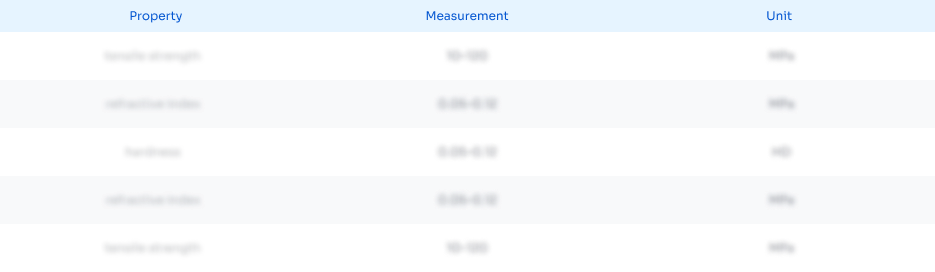
Abstract
Description
Claims
Application Information

- R&D
- Intellectual Property
- Life Sciences
- Materials
- Tech Scout
- Unparalleled Data Quality
- Higher Quality Content
- 60% Fewer Hallucinations
Browse by: Latest US Patents, China's latest patents, Technical Efficacy Thesaurus, Application Domain, Technology Topic, Popular Technical Reports.
© 2025 PatSnap. All rights reserved.Legal|Privacy policy|Modern Slavery Act Transparency Statement|Sitemap|About US| Contact US: help@patsnap.com