Electronically controlled prosthetic knee
a prosthetic knee and electric control technology, applied in the field of prosthetic joints, can solve the problems of changing frictional characteristics, unreliable damping performance, difficult control, etc., and achieve the effects of damping knee joint rotation, wide dynamic torque range, and quick control of lower limb movemen
- Summary
- Abstract
- Description
- Claims
- Application Information
AI Technical Summary
Benefits of technology
Problems solved by technology
Method used
Image
Examples
Embodiment Construction
[0071]Understanding normal human walking / running provides the basis for the design and development of effective lower limb prostheses with controlled motion. Normal human locomotion or gait can be described as a series of rhythmical alternating movements of the limbs and trunk which result in the forward progression of the body's center of gravity.
[0072]One typical gait cycle, as schematically depicted in FIG. 1, comprises of the activity that occurs between heel strike of one lower limb 10 and the subsequent heel strike of the same limb 10. The limb or leg 10 generally comprises a foot 12 and a shin portion 14 coupled or articulated to a thigh portion 16 via a knee or knee joint 18. During a single gait cycle each lower limb or extremity passes through one stance or extended phase 20 and one swing phase 22.
[0073]The stance phase 20 begins at heel-strike 24 when the heel touches the floor or supporting ground surface and the stance knee begins to flex slightly. This flexion allows f...
PUM
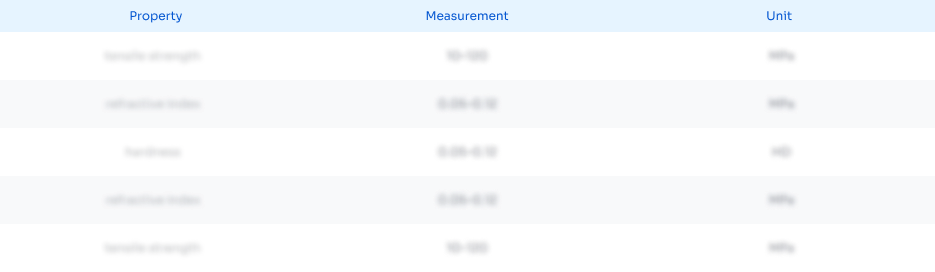
Abstract
Description
Claims
Application Information

- Generate Ideas
- Intellectual Property
- Life Sciences
- Materials
- Tech Scout
- Unparalleled Data Quality
- Higher Quality Content
- 60% Fewer Hallucinations
Browse by: Latest US Patents, China's latest patents, Technical Efficacy Thesaurus, Application Domain, Technology Topic, Popular Technical Reports.
© 2025 PatSnap. All rights reserved.Legal|Privacy policy|Modern Slavery Act Transparency Statement|Sitemap|About US| Contact US: help@patsnap.com