Vacuum pump system
a vacuum pump and pump technology, applied in the direction of pump control, pump components, rotary/oscillating piston combinations for elastic fluids, etc., can solve the problems of unnecessarily high energy expenditure of the pump, negative effect on the service life of the components, and the pump becomes cold, so as to reduce the sound level of the pump system, reduce the noise emission, and reduce the load
- Summary
- Abstract
- Description
- Claims
- Application Information
AI Technical Summary
Benefits of technology
Problems solved by technology
Method used
Image
Examples
Embodiment Construction
[0024]FIG. 1 shows a vacuum pump system 1 having a lock chamber 10 and parallel-connected pumps P1-P5 each of which is connected on its inlet side with the lock chamber. In addition, the vacuum pump system 1 comprises valves V1-V5, by means of which the connection from the pump inlets of the pumps P1-P5 to the lock chamber 10 can be disconnected. The illustrated vacuum pump system is known from prior art. During a pumping-out period the valves V1-V5 are open. The pumps P1-P5 consume a lot of power during the pumping-out period and operate at full speed. The pressure in the lock chamber decreases continuously.
[0025]During an idle period the valves V1-V5 are dosed and the pumps P1-P5 operate at full speed, wherein the power consumption essentially corresponds to that of the operation at a discharge pressure and continues to be relatively high. The pressure in the lock chamber is equal to a transfer pressure.
[0026]During a hold period the valves V1-V5 are open and the pumps P1-P5 opera...
PUM
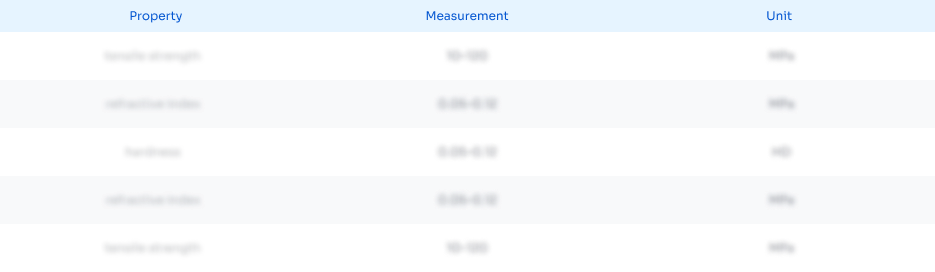
Abstract
Description
Claims
Application Information

- R&D
- Intellectual Property
- Life Sciences
- Materials
- Tech Scout
- Unparalleled Data Quality
- Higher Quality Content
- 60% Fewer Hallucinations
Browse by: Latest US Patents, China's latest patents, Technical Efficacy Thesaurus, Application Domain, Technology Topic, Popular Technical Reports.
© 2025 PatSnap. All rights reserved.Legal|Privacy policy|Modern Slavery Act Transparency Statement|Sitemap|About US| Contact US: help@patsnap.com