Electric cable structural body, electric connection structure, and method for producing electric cable structural body
- Summary
- Abstract
- Description
- Claims
- Application Information
AI Technical Summary
Benefits of technology
Problems solved by technology
Method used
Image
Examples
example 3
[0201]In a vehicle such an automobile or the like, a wire harness connection structure 100 mutually connecting a power source, a control device such as an ECU (Engine Control Unit) and an electric device such as an audio device, a direction indicator or the like includes, as shown in FIG. 22, a wire harnesses W and a branch connector 110 connecting the wire harness W.
[0202]The wire harness W includes a backbone harness Wm connected with the power source or the control device, and branch harnesses Ws that are each branched from the backbone harness Wm and has, at an end thereof, a connector C connected with each of electric devices. The branch connector 110 is connected with at least one of the backbone harness Wm and the branch harnesses Ws.
[0203]With reference to FIG. 23 through FIG. 27, the branch connector 110 in the harness connection structure 100 will be described in detail.
[0204]As shown in FIG. 23 through FIG. 27, the branch connector 110 includes an electric cable group int...
example 1
Production Method Example 1
[0218]First, in an insulating cover removal step, for example, laser light L is directed toward a predetermined portion of the first covered electric cable 131A to remove a predetermined position in the insulating cover 133A. The predetermined portion extends in the longitudinal direction, and the insulating cover 133A in this portion is removed along the entirety of a surface thereof in the circumferential direction. As a result, the core wire 132A is exposed in the conductor exposed portion 132A1. Similarly, the insulating cover 133B is removed from the second covered electric cable 131B to expose the core wire 132B in the conductor exposed portion 132B1.
[0219]In an intersection positional arrangement step, the first covered electric cable 131A and the second covered electric cable 1313 are put to overlap each other such that the conductor exposed portion 132A1 of the first covered electric cable 131A and the conductor exposed portion 132B1 of the second...
example 2
Production Method Example 2
[0266]Now, a method for producing the intersecting electric cable group 130 different from production example 1 will be described in detail with reference to FIGS. 29A and 29B through FIG. 31. In this example also, the first covered electric cable 131A and the second covered electric cable 131B are welded together in the conductor joining step to form the intersecting electric cable group 130.
[0267]The elements identical with those of production method example 1 will bear the same reference signs, and detailed descriptions thereof will be omitted. FIGS. 29A and 29B show the conductor joining step in which the conductor exposed portions 132A1 and 132B1 are jointed together by laser irradiation. FIG. 30 shows the conductor joining step in which the conductor exposed portions 132A1 and 132B1 are jointed together by laser irradiation. FIG. 30 shows the covered electric cables 131 intersecting each other, and one of the covered electric cables 131 is shown with...
PUM
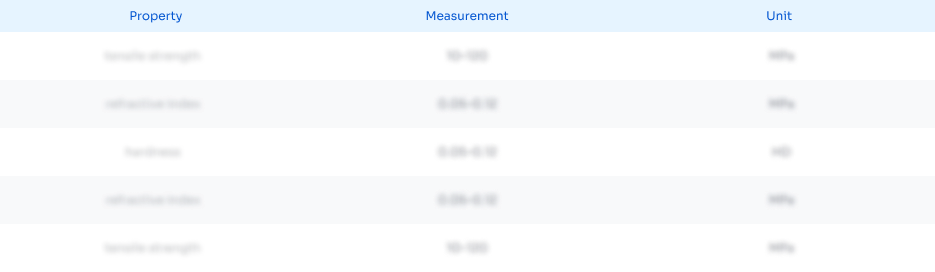
Abstract
Description
Claims
Application Information

- R&D
- Intellectual Property
- Life Sciences
- Materials
- Tech Scout
- Unparalleled Data Quality
- Higher Quality Content
- 60% Fewer Hallucinations
Browse by: Latest US Patents, China's latest patents, Technical Efficacy Thesaurus, Application Domain, Technology Topic, Popular Technical Reports.
© 2025 PatSnap. All rights reserved.Legal|Privacy policy|Modern Slavery Act Transparency Statement|Sitemap|About US| Contact US: help@patsnap.com