Method for minimizing the gap between a rotor and a housing
a technology of rotor blade and housing, which is applied in the direction of liquid fuel engines, machines/engines, mechanical equipment, etc., can solve the problems of low efficiency, high equipment cost, and inability to meet the needs of maintenance, and achieve the effect of simple means, increased power output, and consequently maximized turbine efficiency
- Summary
- Abstract
- Description
- Claims
- Application Information
AI Technical Summary
Benefits of technology
Problems solved by technology
Method used
Image
Examples
Embodiment Construction
[0025]The FIGURE shows a turbine 100, in this case a gas turbine, in a longitudinal partial section. Inside, the gas turbine 100 has rotor 103 which is rotatably mounted around a rotational axis 102 (axial direction) and which is also referred to as a turbine rotor.
[0026]Arranged in series along the rotor 103 are an intake housing 104, a compressor 105, a toroidal combustion chamber 110—especially an annular combustion chamber 106—with a plurality of coaxially arranged burners 107, a turbine 108 and the exhaust gas housing 109.
[0027]The annular combustion chamber 106 communicates with an annular hot gas passage 111. Four series-connected turbine stages 112, for example, form the turbine 108 there. Each turbine stage 112 is formed from two blade rings. In the hot gas passage 111, a row 125 formed from rotor blades 120 follows a stator blade row 115, as seen in the flow direction of a working medium 113.
[0028]The stator blades 130 are fastened on the stator 143 in this case, whereas t...
PUM
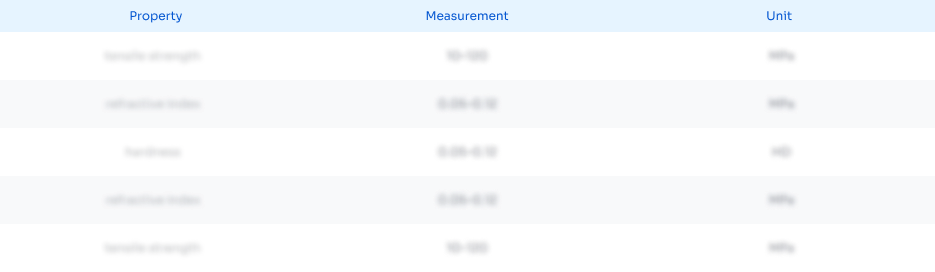
Abstract
Description
Claims
Application Information

- R&D
- Intellectual Property
- Life Sciences
- Materials
- Tech Scout
- Unparalleled Data Quality
- Higher Quality Content
- 60% Fewer Hallucinations
Browse by: Latest US Patents, China's latest patents, Technical Efficacy Thesaurus, Application Domain, Technology Topic, Popular Technical Reports.
© 2025 PatSnap. All rights reserved.Legal|Privacy policy|Modern Slavery Act Transparency Statement|Sitemap|About US| Contact US: help@patsnap.com