Fixed cutter drill bit heel and back-ream cutter protections for abrasive applications
a technology of fixed cutter and protection, which is applied in the direction of cutting machines, manufacturing tools, other chemical processes, etc., can solve the problems of significant wear to the heel surface of fixed cutters, inability to justify their higher cost, and wear to the gage region of fixed cutters
- Summary
- Abstract
- Description
- Claims
- Application Information
AI Technical Summary
Benefits of technology
Problems solved by technology
Method used
Image
Examples
Embodiment Construction
[0027]In one aspect, embodiments disclosed herein relate generally to fixed cutter drill bits. More particularly, embodiments disclosed herein relate to fixed cutter drill bit heel and back-ream cutter protections for abrasive applications.
[0028]According to embodiments of the present disclosure, the heel surface and gage region of a fixed cutter bit may be provided with a unique combination of materials in order to add protection for that particular area of the bit, and thus increase the life of the bit. As described in more detail below, methods of increasing heel surface and gage protection may include forming a fixed cutter bit using a combination of back reaming elements and a matrix material different from other regions of the bit.
[0029]For example, a drill bit according to some embodiments of the present disclosure is shown in FIGS. 2A and 2B. As shown, a drill bit 200 has a longitudinal axis L, a threaded pin connection 205 and a cutting face 210. A plurality of blades 220 a...
PUM
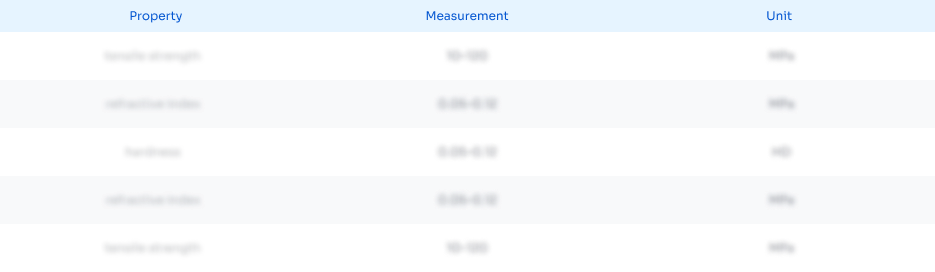
Abstract
Description
Claims
Application Information

- R&D
- Intellectual Property
- Life Sciences
- Materials
- Tech Scout
- Unparalleled Data Quality
- Higher Quality Content
- 60% Fewer Hallucinations
Browse by: Latest US Patents, China's latest patents, Technical Efficacy Thesaurus, Application Domain, Technology Topic, Popular Technical Reports.
© 2025 PatSnap. All rights reserved.Legal|Privacy policy|Modern Slavery Act Transparency Statement|Sitemap|About US| Contact US: help@patsnap.com