Heat sink with heat bus and fin structure
- Summary
- Abstract
- Description
- Claims
- Application Information
AI Technical Summary
Benefits of technology
Problems solved by technology
Method used
Image
Examples
second embodiment
[0027]FIG. 3 is a section end view of alternate second embodiment of a heat sink 10 of the present invention, where the heat sink is secured over the processor 20. The heat sink 10 comprises a honeycomb fin structure 12 coupled to a U-shaped heat bus 14 having a first leg 21 having a first side 15 and a second side 11 that generally conforms to the side 16 of the fin structure 12 disposed adjacent to the first leg 21. The U-shaped heat bus 14 further comprises a second leg 23 having a first side 15 and a second side 11 that generally conforms to the side 16 of the fin structure 12 adjacent to the second leg 23. The second sides 11 of the first leg 21 and the second leg 23 of the embodiment of the U-shaped heat bus 14 of FIG. 3 are in generally uninterrupted contact with the sides 16 of the fin structure 12, and perhaps generally continuously connected to the sides 16, to enhance conductive heat transfer from the first leg 21 and the second leg 23 of the U-shaped heat bus 14 to the f...
third embodiment
[0028]FIG. 4 is a perspective view of a heat sink 10 of the present invention comprising a honeycomb fin structure 12 coupled to a U-shaped heat bus 14 having a base 26, a plurality of first legs 21 and a plurality of second legs 23 (partially shown) along the opposing side of the fin structure. The first legs 21 and the second legs 23 are connected to the landings 19 on the sides 16 of the fin structure 12 by connections 18 to further enhance distribution of heat from the processor (not shown), through the base 26 and the first legs 21 and second legs 23 of the heat bus 14 to the fin structure 12. The first legs 21 are illustrated in FIG. 4 as being parallel and generally equally spaced along the length of the fin structure 12 between the inlet end 24 and the outlet end 25 of the air channels 15 therein.
fourth embodiment
[0029]FIG. 5A is a perspective view of a heat sink 10 of the present invention comprising a honeycomb fin structure 12 coupled to a U-shaped heat bus 14 having a base 26, a first leg 21 having a width 48 and a second leg 23 (partially shown) extending from the base 26 and connected to landings 19 on the fin structure 12 by connections 18. The first leg 21 and the second leg 23 of the heat bus 14 shown in FIG. 5A have a broad profile or width 48 to further enhance distribution of heat from the processor (not shown), through the base 26 and the first leg 21 and second leg 23 of the heat bus 14 to the fin structure 12. It will be understood that other embodiments of the heat sink 10 may comprise a heat bus 14 having a first leg and a second leg that are as wide (dimension 48) as the fin structure 10 is long from the inlet end 24 to the outlet end 25.
[0030]FIG. 5B is a perspective view of a modified fourth embodiment of the heat sink 10 of FIG. 5A comprising a honeycomb fin structure 12...
PUM
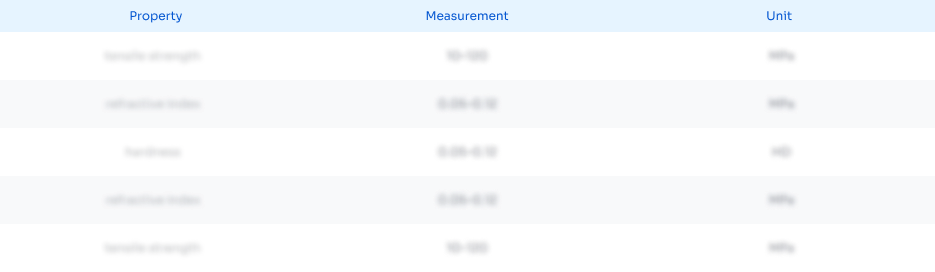
Abstract
Description
Claims
Application Information

- R&D
- Intellectual Property
- Life Sciences
- Materials
- Tech Scout
- Unparalleled Data Quality
- Higher Quality Content
- 60% Fewer Hallucinations
Browse by: Latest US Patents, China's latest patents, Technical Efficacy Thesaurus, Application Domain, Technology Topic, Popular Technical Reports.
© 2025 PatSnap. All rights reserved.Legal|Privacy policy|Modern Slavery Act Transparency Statement|Sitemap|About US| Contact US: help@patsnap.com