Pad conditioning force modeling to achieve constant removal rate
a technology of force modeling and conditioning disk, which is applied in the direction of abrasive surface conditioning devices, lapping machines, manufacturing tools, etc., can solve the problems of drifting polishing pad effectiveness, affecting the uniformity of the results from substrate to substrate, and the effect of the conditioning disk is reduced
- Summary
- Abstract
- Description
- Claims
- Application Information
AI Technical Summary
Benefits of technology
Problems solved by technology
Method used
Image
Examples
Embodiment Construction
[0015]Embodiments of the invention are directed towards the performance of a CMP polishing pad. Embodiments of the disclosure provide a method and apparatus for controlling a CMP polisher based on a relationship between conditioning arm sweep torque and friction between the polishing pad and conditioning disk. Embodiments include a method for adjusting a down-force (down force) applied by a conditioning disk to a polishing pad based on a difference between a measured force and a modeled force profile to improve processing results. It is contemplated that aspects of the present disclosure that enable use of conditioner sweep torque to monitor polisher performance may be applied in real time and / or when the polishing pad is being conditioned while a substrate is being polished (i.e., in-situ conditioning), when the polishing pad is conditioned in-between substrate polishing (i.e., ex-situ conditioning), or any combination thereof.
[0016]FIG. 1 is a sectional view of one embodiment of a...
PUM
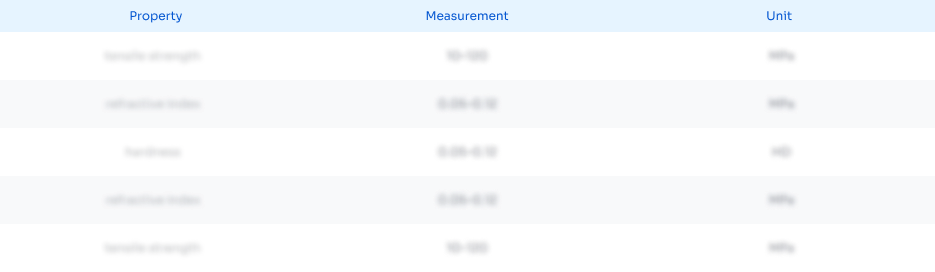
Abstract
Description
Claims
Application Information

- R&D
- Intellectual Property
- Life Sciences
- Materials
- Tech Scout
- Unparalleled Data Quality
- Higher Quality Content
- 60% Fewer Hallucinations
Browse by: Latest US Patents, China's latest patents, Technical Efficacy Thesaurus, Application Domain, Technology Topic, Popular Technical Reports.
© 2025 PatSnap. All rights reserved.Legal|Privacy policy|Modern Slavery Act Transparency Statement|Sitemap|About US| Contact US: help@patsnap.com