Multi-purpose mobile modular structure
a mobile, modular technology, applied in the direction of structural elements, building components, load-supporting elements, etc., can solve the problems of difficult transportation to the site of use, limited configurations obtainable using shipping containers, and similar problems in assembly processes, so as to achieve the effect of drastically reducing the difficulty of manufacturing, handling, storage and transportation of modular structures
- Summary
- Abstract
- Description
- Claims
- Application Information
AI Technical Summary
Benefits of technology
Problems solved by technology
Method used
Image
Examples
embodiment 2
[0141]FIG. 13 is the perspective view of the embodiment 2 of the present invention which relates to the frame assembly of the modular structure, FIG. 14 is the cross-sectional view of FIG. 13, FIG. 15 shows the joints being used for the frame assembly in FIG. 13, FIG. 16 shows the center joint being used in the frame assembly in FIG. 13. Because the basic structure of this embodiment is the same as that of embodiment 1, the structural components are numbered similarly and also added with an “A” and detailed explanation is omitted.
[0142]The frame assembly 1A for this embodiment is similar to FIGS. 13 and 14, end joint 135 and the center joint 137 are used for expansion of the structure. In this embodiment, the outer frame sections 19A of the upper section 13A, the lower section 15A and the side section 17A form four cavities 23A.
[0143]The said end joint 135, as shown in FIGS. 13 to 15, is affixed between two end joints 9 on either side and together with said end joints 9 form the “C”...
modified embodiment
[0150]In this embodiment, as shown in FIG. 17, by using the end joint 135 and the center joint 137 appropriately, the frame assembly 1B can be further expanded. In this modified embodiment, the outer frame section 19A of the upper section 13A and the lower section 15A and the side section 17A form nine cavities 23B.
[0151]Accordingly, in the frame assembly 1B, the use of the end joint 135 and the center joint 137 to further expand the structure also allows it to distribute the load even further.
embodiment 3
[0152]FIGS. 18 to 27 show the joints involved in embodiment 3 of the current invention. In this embodiment, because of the similarity to embodiments 1 and 2, the numbering of the respective component will be the same with the substitution of “C” for “A” and detailed descriptions will be omitted.
[0153]In this embodiment, as shown in FIGS. 18 to 27, joints 139, 140, 149, 157, 161, 165, 167, 171, 175, 179 can be used to further augment the frame assembly and also the form of the frame assembly in added flexibility.
[0154]The joint 139 in FIG. 18 is an end joint that is essentially the end joint 9 in embodiment 1 added with an end support sleeve 141 in the rear face.
[0155]That is, joint 139 is formed by the end support sleeve 141 on the vertical wall 55 on the rear face of end support joint 73C. With this, joint 139 forms a “T” shape body when viewed from the top and also from the side.
[0156]The said end support sleeve 141 is longer than the end support joint 71C. End support sleeve 141 ...
PUM
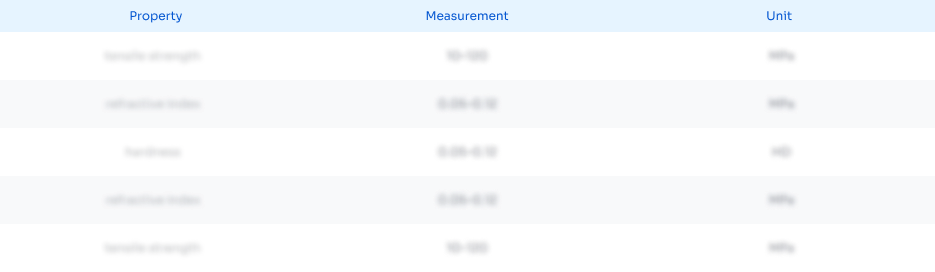
Abstract
Description
Claims
Application Information

- R&D
- Intellectual Property
- Life Sciences
- Materials
- Tech Scout
- Unparalleled Data Quality
- Higher Quality Content
- 60% Fewer Hallucinations
Browse by: Latest US Patents, China's latest patents, Technical Efficacy Thesaurus, Application Domain, Technology Topic, Popular Technical Reports.
© 2025 PatSnap. All rights reserved.Legal|Privacy policy|Modern Slavery Act Transparency Statement|Sitemap|About US| Contact US: help@patsnap.com