Heat exchanger apparatus
a technology of heat exchangers and baffles, which is applied in the direction of indirect heat exchangers, machines/engines, lighting and heating apparatus, etc., can solve the problems of increasing the likelihood of flow induced tube vibration, affecting the efficiency of heat exchangers, so as to reduce the pitch dimension of tubes, reduce the size of baffles, and reduce the effect of pressure loss
- Summary
- Abstract
- Description
- Claims
- Application Information
AI Technical Summary
Benefits of technology
Problems solved by technology
Method used
Image
Examples
Embodiment Construction
[0028]Referring to FIG. 1, a schematic of a solar power plant 200 is illustrated according to an embodiment of the present invention. While the invention is discussed in terms of (or incorporated into) a solar power plant 200, the invention is not so limited and can be used in any environment in which a superheater, preheater or other heat exchanger apparatus is required.
[0029]The solar power plant 200 generally comprises a preheater 10, a steam generator 20, a superheater 30, a high pressure (HP) turbine 40, a reheater 50, a low pressure (LP) turbine 45, an air cooled condenser 60, a condensate pump 65, a low pressure feedwater heater 70, a deaerator 80, a boiler feed pump 85 and a high pressure feedwater heater 90. All of the aforementioned components of the solar power plant 200 are arranged and operably coupled to one another as is known in the art.
[0030]In the solar power plant 200, the preheater 10 is used to preheat a secondary fluid, which is water in the exemplified embodim...
PUM
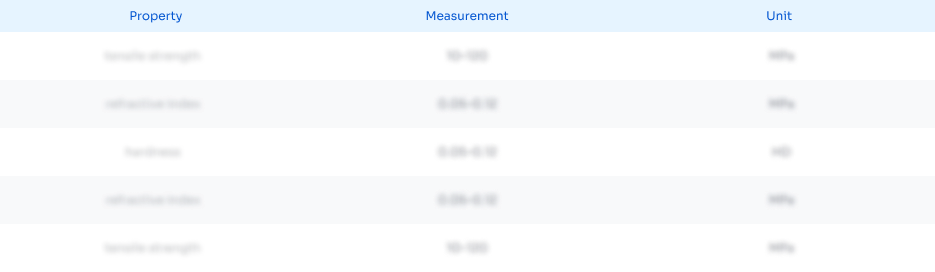
Abstract
Description
Claims
Application Information

- R&D
- Intellectual Property
- Life Sciences
- Materials
- Tech Scout
- Unparalleled Data Quality
- Higher Quality Content
- 60% Fewer Hallucinations
Browse by: Latest US Patents, China's latest patents, Technical Efficacy Thesaurus, Application Domain, Technology Topic, Popular Technical Reports.
© 2025 PatSnap. All rights reserved.Legal|Privacy policy|Modern Slavery Act Transparency Statement|Sitemap|About US| Contact US: help@patsnap.com