Bitumen froth treating process
- Summary
- Abstract
- Description
- Claims
- Application Information
AI Technical Summary
Benefits of technology
Problems solved by technology
Method used
Image
Examples
Embodiment Construction
[0082]The present invention is directed at a process for treating bitumen froth which provides for first gravity separation of a first mixture comprising the bitumen froth and a first amount of a paraffinic solvent into a first overflow stream and a first underflow stream, wherein the first mixture is comprised of first mixture asphaltenes, and wherein the first underflow stream is comprised of less than or equal to about 40 percent of the first mixture asphaltenes by weight. Stated otherwise, the first gravity separation results in precipitation and / or rejection from the first overflow stream of less than or equal to about 40 percent of the first mixture asphaltenes by weight.
[0083]As a result, the process of the invention may be distinguished from typical commercial paraffinic froth treatment processes which typically provide for between about 40 percent and about 50 percent asphaltene precipitation and / or rejection by weight in a first separation stage.
[0084]The relatively lower ...
PUM
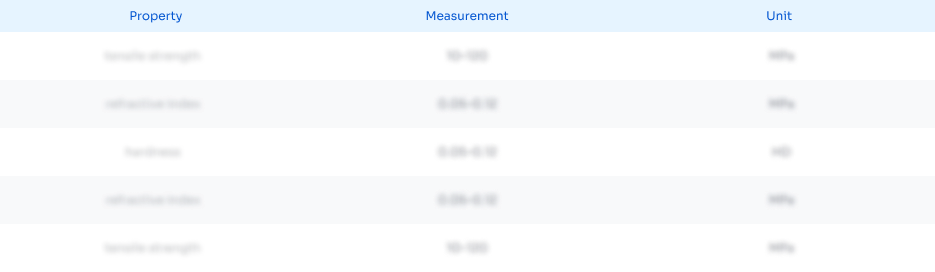
Abstract
Description
Claims
Application Information

- R&D
- Intellectual Property
- Life Sciences
- Materials
- Tech Scout
- Unparalleled Data Quality
- Higher Quality Content
- 60% Fewer Hallucinations
Browse by: Latest US Patents, China's latest patents, Technical Efficacy Thesaurus, Application Domain, Technology Topic, Popular Technical Reports.
© 2025 PatSnap. All rights reserved.Legal|Privacy policy|Modern Slavery Act Transparency Statement|Sitemap|About US| Contact US: help@patsnap.com