Refrigerant system with economizer, intercooler and multi-stage compressor
a refrigeration system and compressor technology, applied in the direction of gas cycle refrigeration machines, compression machines with cascade operation, refrigeration machines, etc., can solve the problems of less practicability of intercooler provision, exceeding safety or reliability limits, and extremely high refrigerant discharge temperature, etc., to improve the performance of the refrigerant system, the effect of enhancing heat rejection capability and increasing temperature differential
- Summary
- Abstract
- Description
- Claims
- Application Information
AI Technical Summary
Benefits of technology
Problems solved by technology
Method used
Image
Examples
Embodiment Construction
[0017]A refrigerant system 20 is illustrated in FIG. 1. Three stages of compression 24, 26, and 28 are positioned in series within the refrigerant system 20 to progressively compress refrigerant from suction to discharge pressure. Although a multi-stage compressor system is represented by separate compressor units that are disposed in series, as shown in FIG. 1, separate compression members can be utilized instead of some or all of the compressor units. Specifically, for instance, in the case of a three-stage reciprocating compressor, the three separate compression members may represent different banks of cylinders connected in series. Refrigerant, compressed by the first stage from a suction pressure to a first intermediate pressure, is delivered from a discharge outlet of this first stage to the suction inlet of the second stage. Refrigerant vapor is compressed by the second stage to a second intermediate pressure and delivered from a discharge outlet of this second stage to the s...
PUM
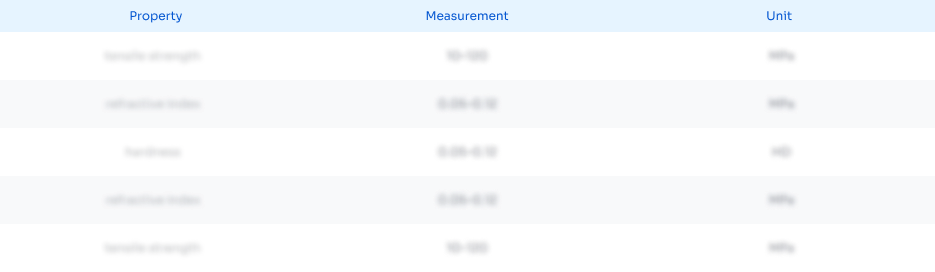
Abstract
Description
Claims
Application Information

- R&D
- Intellectual Property
- Life Sciences
- Materials
- Tech Scout
- Unparalleled Data Quality
- Higher Quality Content
- 60% Fewer Hallucinations
Browse by: Latest US Patents, China's latest patents, Technical Efficacy Thesaurus, Application Domain, Technology Topic, Popular Technical Reports.
© 2025 PatSnap. All rights reserved.Legal|Privacy policy|Modern Slavery Act Transparency Statement|Sitemap|About US| Contact US: help@patsnap.com