Air supply system with reduced oil passing in compressor
- Summary
- Abstract
- Description
- Claims
- Application Information
AI Technical Summary
Benefits of technology
Problems solved by technology
Method used
Image
Examples
Embodiment Construction
[0032]Referring first to FIG. 1, an air supply system 10 in accordance with an embodiment of the present invention is shown. Air supply system 10 includes a compressor 12 having a compression chamber 14, a compressor head 15, an inlet port 16 through which air flows into compression chamber 14 and an outlet port 18 through which air exits compression chamber 14. Compressor 12 is typically a reciprocating type compressor, and may have any of numerous known or yet to be developed configurations, the particular configuration thereof being generally unimportant to operation of the invention disclosed herein. Since numerous such compressors are extremely well-known in the art, the particular structure and operation of compressor 12 is not discussed herein in detail.
[0033]An unloader 20 causes compressor 12 to be in an unloaded state in response to a pneumatic signal being received at a signal port 22 thereof. Unloader 20 may be integrally formed as part of compressor 12 (as shown in the ...
PUM
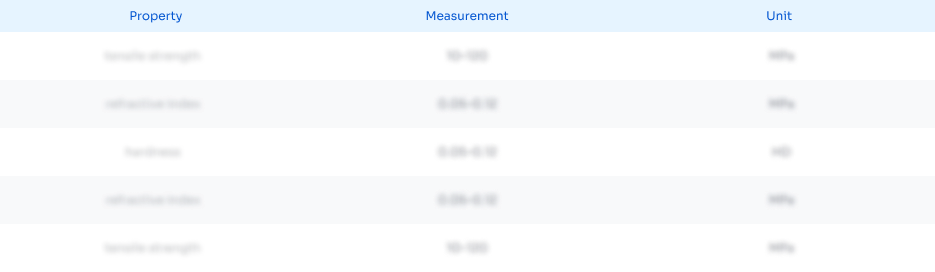
Abstract
Description
Claims
Application Information

- R&D
- Intellectual Property
- Life Sciences
- Materials
- Tech Scout
- Unparalleled Data Quality
- Higher Quality Content
- 60% Fewer Hallucinations
Browse by: Latest US Patents, China's latest patents, Technical Efficacy Thesaurus, Application Domain, Technology Topic, Popular Technical Reports.
© 2025 PatSnap. All rights reserved.Legal|Privacy policy|Modern Slavery Act Transparency Statement|Sitemap|About US| Contact US: help@patsnap.com