Coated fibrous nodules and insulation product
a technology of applied in the field of coated fibrous nodules and insulation products, can solve the problems of slowing down the installation process, affecting the installation process,
- Summary
- Abstract
- Description
- Claims
- Application Information
AI Technical Summary
Problems solved by technology
Method used
Examples
example 1
[0054]Nodules formed from glass fibers were provided which were mostly roughly spherical in shape and had an average diameter or length of about ¼ inch. A majority of the nodules had a maximum dimension of ½ inch or less. The glass fibers had an average diameter of 2.0 microns and contained B2O3 in an amount of 8.7 wt. %. The glass fibers had on their surface a silicone agent in an amount of 0.05 wt. % and a de-dusting oil in an amount of 0.06 wt. %, based on the weight of the glass fibers.
[0055]A blowing machine available from Unisul under the trade name Volumatic® III, was used to blow the nodules at a wall cavity. The blowing machine was equipped with 150 feet of 4-inch diameter hose and provided a nodule mass flow rate of approximately 18 lbs / min. The blowing machine was operated with the transmission in third gear with 100% of the available blower air delivered to the rotary airlock assembly and with the slide gate (feed gate) set at 12 inches. The blower and secondary gearbox ...
example 2
[0063]Insulation was formed in the same manner as described in Example 1, except that the nozzle was positioned two feet from the cavity instead of six feet from the cavity during application of the coated nodules to the cavity. The results are set forth in the following Table 2.
TABLE 2Installation Using a Nozzle Position Two Feet from the CavitySample 8Sample 5Sample 6Sample 7(2 by 6 in,(2 by 4 in,(2 by 4 in,(2 by 6 in,2416 in OC)24 in OC)16 in OC)in OC)Ratio of Binder Solution0.24–0.260.24–0.260.24–0.260.24–0.26to Dry NodulesJust-Installed Moisture,20–3020–3020–3020–30wt. %Just-installed Amount of1.0–1.51.5–2.31.5–2.32.4–3.6Water per Cavity,lbs / cavityInstallation Time,21323351sec / cavityDry Insulation Density,1.7–1.81.7.–1.81.7–1.81.7–1.8PCFR-value15152323
[0064]In comparing the results shown in Tables 1 and 2, applying the coated nodules with a 6-foot distance between the nozzle and the cavity resulted in an insulation density of from 0.8 to 0.9 PCF, whereas applying the coated nod...
example 3
[0065]Insulation was formed in the same manner as described in Example 1, except that the slide gate on the blowing machine was set to 7 inches, i.e., about 40% open. At such setting, the mass flow rate of the dry nodules was about 10 lbs / min instead of the 18 lbs / min flow rate employed in Example 1. The results of such tests are set forth in the following Table 3.
TABLE 3Installation Using a Reduced Nodule Flow RateSample 9Sample 10Sample 11Sample 12(2 by 4 in, 16(2 by 4 in, 24(2 by 6 in,(2 by 6 in, 24in OC)in OC)16 in OC)in OC)Ratio of Binder Solution to0.43–0.530.43–0.530.43–0.530.43–0.53Dry NodulesJust-Installed Moisture,45454545wt. %Just-installed Amount of1.21.91.93Water per Cavity,lbs / cavityInstallation Time,15202029sec / cavityDry Insulation Density,0.8–0.90.8–0.90.8–0.90.8–0.9PCFR-value13132020
[0066]As can be seen from Table 3, due to the reduced flow rate of the dry nodules, the ratio of the binder solution to the dry nodules was higher in comparison with the ratios obtained ...
PUM
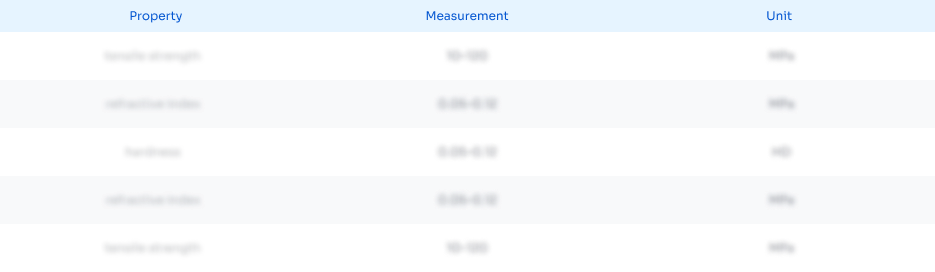
Abstract
Description
Claims
Application Information

- R&D
- Intellectual Property
- Life Sciences
- Materials
- Tech Scout
- Unparalleled Data Quality
- Higher Quality Content
- 60% Fewer Hallucinations
Browse by: Latest US Patents, China's latest patents, Technical Efficacy Thesaurus, Application Domain, Technology Topic, Popular Technical Reports.
© 2025 PatSnap. All rights reserved.Legal|Privacy policy|Modern Slavery Act Transparency Statement|Sitemap|About US| Contact US: help@patsnap.com