Vibration control of free piston machines through frequency adjustment
a free piston machine and frequency adjustment technology, applied in the direction of piston pumps, pump parameters, domestic cooling apparatus, etc., can solve the problems of unconfined by conventional crankshafts and connecting rods, reciprocating machines cause substantial vibration, and vibration is ordinarily undesirable, so as to reduce or minimize the amplitude of mechanical vibration of mechanical apparatus
- Summary
- Abstract
- Description
- Claims
- Application Information
AI Technical Summary
Benefits of technology
Problems solved by technology
Method used
Image
Examples
Embodiment Construction
[0027] The invention makes use of the observation that, for a mechanical apparatus that includes a vibrating or reciprocating main machine coupled to a secondary vibrating system, which can include a vibration balancer, there are three frequencies that are important. There are the resonant (or natural) frequency of the vibrating main machine, the resonant (or natural) frequency of the secondary vibrating system and the operating frequency of the main machine. The operating frequency of the main machine is also the operating frequency of the vibration balancer and any other secondary vibrating system coupled to the main machine.
[0028] If a graph is made of frequency vs. amplitude of vibration for any resonant system, the plotted amplitudes form a resonant peak centered at a resonant frequency. These peaks can rise and fall in a range extending from a broad, gradual manner, to a sharp, steep manner. The sharper the peak, the higher the quality factor “Q” of the resonant system, as kn...
PUM
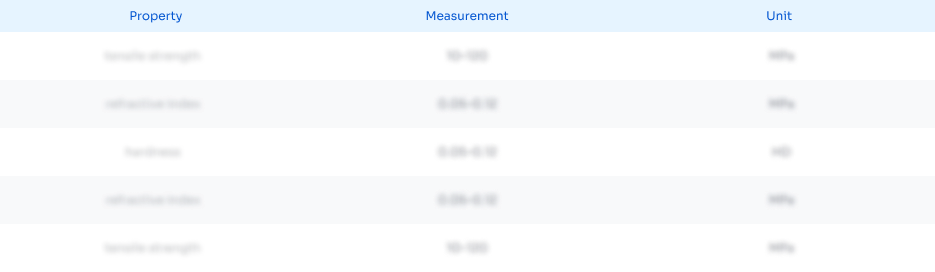
Abstract
Description
Claims
Application Information

- R&D
- Intellectual Property
- Life Sciences
- Materials
- Tech Scout
- Unparalleled Data Quality
- Higher Quality Content
- 60% Fewer Hallucinations
Browse by: Latest US Patents, China's latest patents, Technical Efficacy Thesaurus, Application Domain, Technology Topic, Popular Technical Reports.
© 2025 PatSnap. All rights reserved.Legal|Privacy policy|Modern Slavery Act Transparency Statement|Sitemap|About US| Contact US: help@patsnap.com