Self-regulating temperature control system
a temperature control system and self-regulating technology, applied in the direction of fluid circulation arrangement, refrigeration machines, lighting and heating apparatus, etc., can solve the problems of simply non-competitive cost parameters in the modern marketplace, and not efficient to cool the whole radar array associated, so as to achieve the desired level of operating efficiency and minimize the cost level
- Summary
- Abstract
- Description
- Claims
- Application Information
AI Technical Summary
Benefits of technology
Problems solved by technology
Method used
Image
Examples
Embodiment Construction
[0027] The embodiments described in detail herein below are directed to a self-regulating cooling (or heating) system and method for passively or actively providing a desired level of operating efficiency at a minimized cost level when compared with known cooling and heating systems and methods that employ active control techniques. The self-regulating cooling / heating system and method, as stated herein before, can direct a cooling or heating (fluidic) medium, e.g. liquid, gas, medium that changes state or undergoes a phase transition, through only those portions of a system or device that are operationally hot or cold, while substantially ignoring those portions of the system or device that are not operationally hot or cold or are otherwise operationally cool or hot.
[0028] Before moving to the Figures, it is important to note that the system or device to be cooled or heated is cooled or heated in sections or portions that are independent from one another such that it is possible t...
PUM
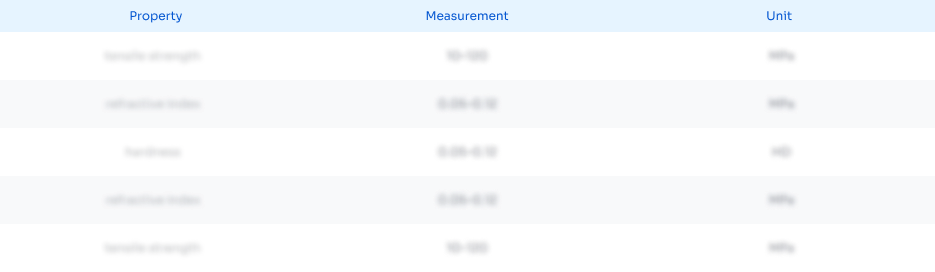
Abstract
Description
Claims
Application Information

- R&D
- Intellectual Property
- Life Sciences
- Materials
- Tech Scout
- Unparalleled Data Quality
- Higher Quality Content
- 60% Fewer Hallucinations
Browse by: Latest US Patents, China's latest patents, Technical Efficacy Thesaurus, Application Domain, Technology Topic, Popular Technical Reports.
© 2025 PatSnap. All rights reserved.Legal|Privacy policy|Modern Slavery Act Transparency Statement|Sitemap|About US| Contact US: help@patsnap.com