Safe incineration of explosive air mixtures
- Summary
- Abstract
- Description
- Claims
- Application Information
AI Technical Summary
Benefits of technology
Problems solved by technology
Method used
Image
Examples
Embodiment Construction
[0015]FIG. 1 illustrates a constant-source-flow fume incineration system embodiment of the present invention, and referred to by the general reference numeral 100. The system 100 is connected to receive a fume source 102 of gases for incineration before discharging them into the atmosphere. A standard flow is received from fume source 102 according to the nature of the source or government operating permits dictating such. A source flowmeter 104 monitors the volume of gases entering and reports its measurements to a system controller 106. A first temperature sensor 108 allows the controller 106 to convert to Standard Conditions for its calculations. A motorized damper 110 is adjusted by the controller 106 to admit more or less ambient air 112 in order to dilute the incoming gases enough to keep their mixture below the lower explosive limit (LEL). Such LEL is the lowest percentage of volatile gases in the air mixture that will explode if exposed to open flames or sparks, or that will...
PUM
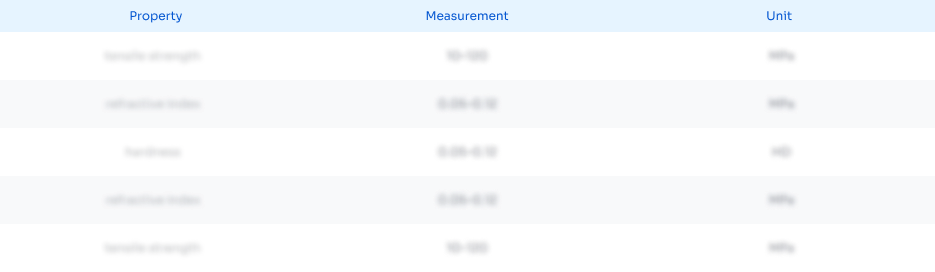
Abstract
Description
Claims
Application Information

- R&D
- Intellectual Property
- Life Sciences
- Materials
- Tech Scout
- Unparalleled Data Quality
- Higher Quality Content
- 60% Fewer Hallucinations
Browse by: Latest US Patents, China's latest patents, Technical Efficacy Thesaurus, Application Domain, Technology Topic, Popular Technical Reports.
© 2025 PatSnap. All rights reserved.Legal|Privacy policy|Modern Slavery Act Transparency Statement|Sitemap|About US| Contact US: help@patsnap.com